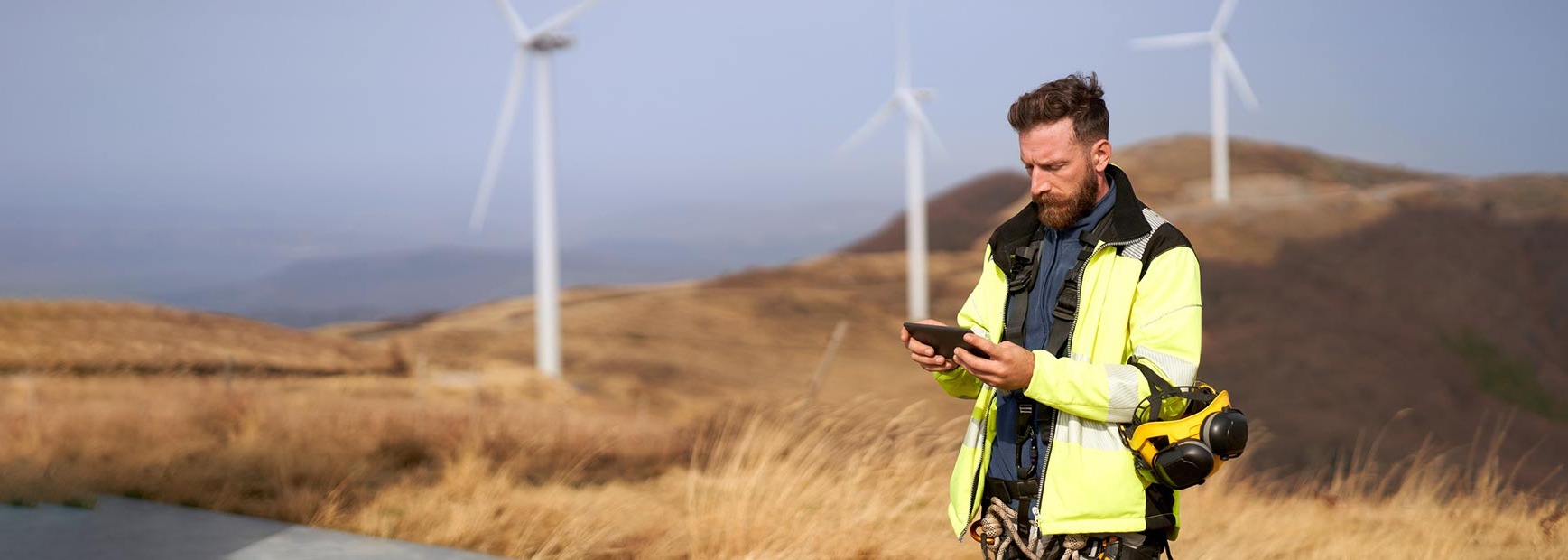
Continuous improvements
– fault finding, simplification and refinement
How we help organisations get better at getting better.
Obstacles when working with continuous improvements
Continuous improvement using Lean and Six Sigma, for example, is commonplace in both large and small organizations across a range of industries. However, all too often there is a lack of a holistic view where the overall goals of the organization, the management system and the improvements can interact. Continuous improvement, and its input and output data, for example, may be in several different systems or even on a physical board that not everyone has access to.
The problem can be summarized as follows:
1
The management system and continuous improvement live separate and unrelated lives.
2
Too many different systems - one for complaints, one for improvement projects, one for the management system, one for internal problem management etc.
3
Not all improvement efforts are documented. .
4
Improvement efforts are carried out locally on different sites, without overview and control from above, which easily leads to sub-optimization.
5
The link between daily activities and ongoing improvement initiatives is poor. In order to get a sufficient link, and overview, one is forced to look for information in several systems and copy data manually.
6
Physical lean boards are still used, but create a gap between the digital and the paper-based. And, you can only access the board's information on site.
Previously, discrepancies were handled manually through Excel and e-mail. We are now transferring more and more of the management to CANEA ONE, which is more efficient and safer. It saves time and, at the same time, everyone knows who owns a task and its status.
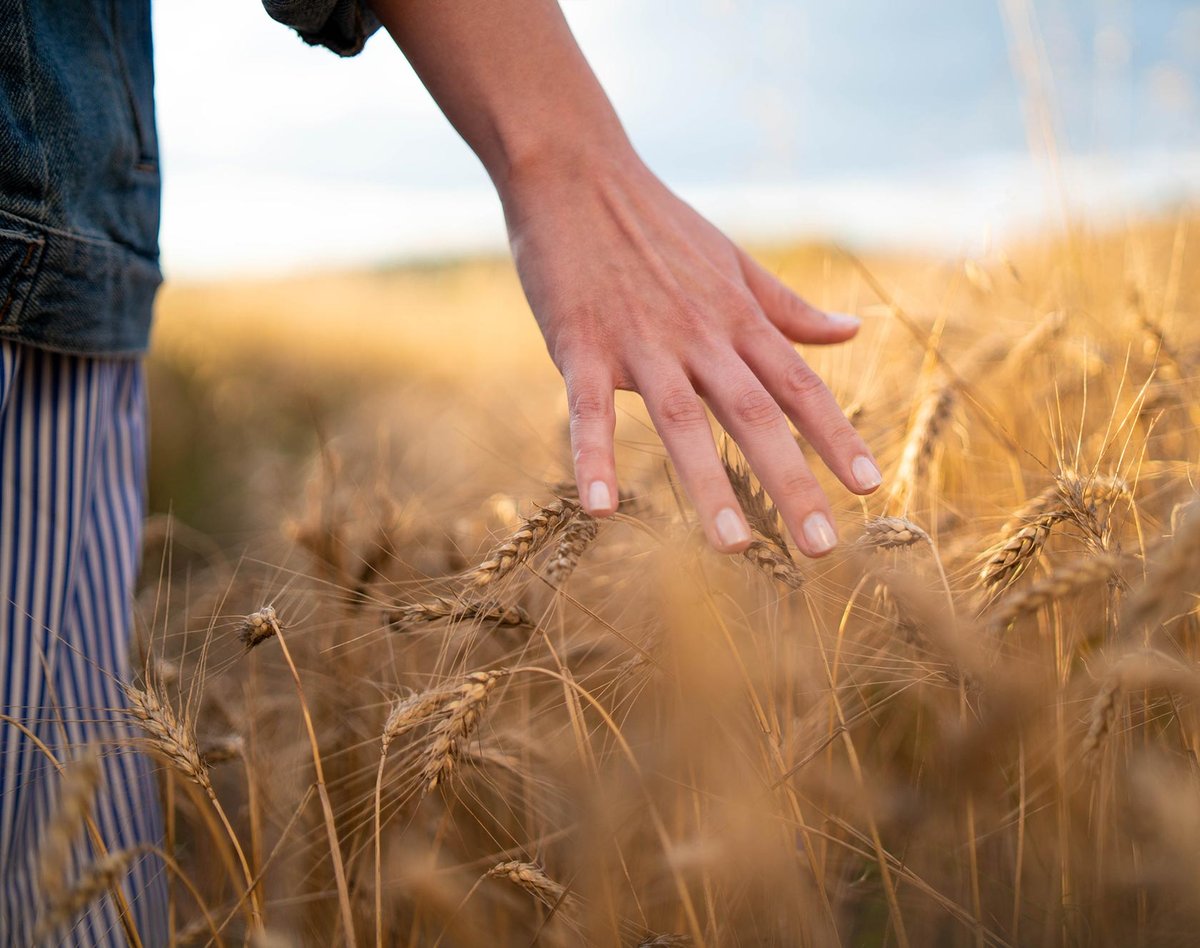
How to increase the efficiency of improvement work
CANEA ONE makes continuous improvement more efficient by collecting and organizing all relevant data in a common system. It provides a good overview of ongoing initiatives, makes governance simpler and more efficient, and facilitates keeping stakeholders informed of what is happening. It also reduces the risk of improvement proposals being left unaddressed and eventually forgotten.
Our solution to the above problem, and what makes many organizations choose CANEA ONE for their continuous improvement, is that:
-
CANEA ONE transforms the continuous improvement process into a fully digital environment, lowering the threshold for initiating and documenting improvement initiatives.
-
All data is collected in one system. This reduces overheads, the time spent searching for information, the risk of information being lost and system costs, while at the same time providing a better overview.
-
Work efficiency increases when it is digitized - relevant information can be distributed to the right people automatically, reminders don't need to be sent manually and initiatives don't risk getting lost on a file server.
-
There will be a shorter path between improvement initiatives and daily operations because digitized improvement initiatives can be interfaced with the management system.
-
Graphs and charts are displayed digitally and are easily accessible, searchable and updated with the latest data points.
-
CANEA ONE is easy to configure, regardless of whether you have chosen PDCA, Lean, Six Sigma, 8D, DMAIC or any other improvement methodology.
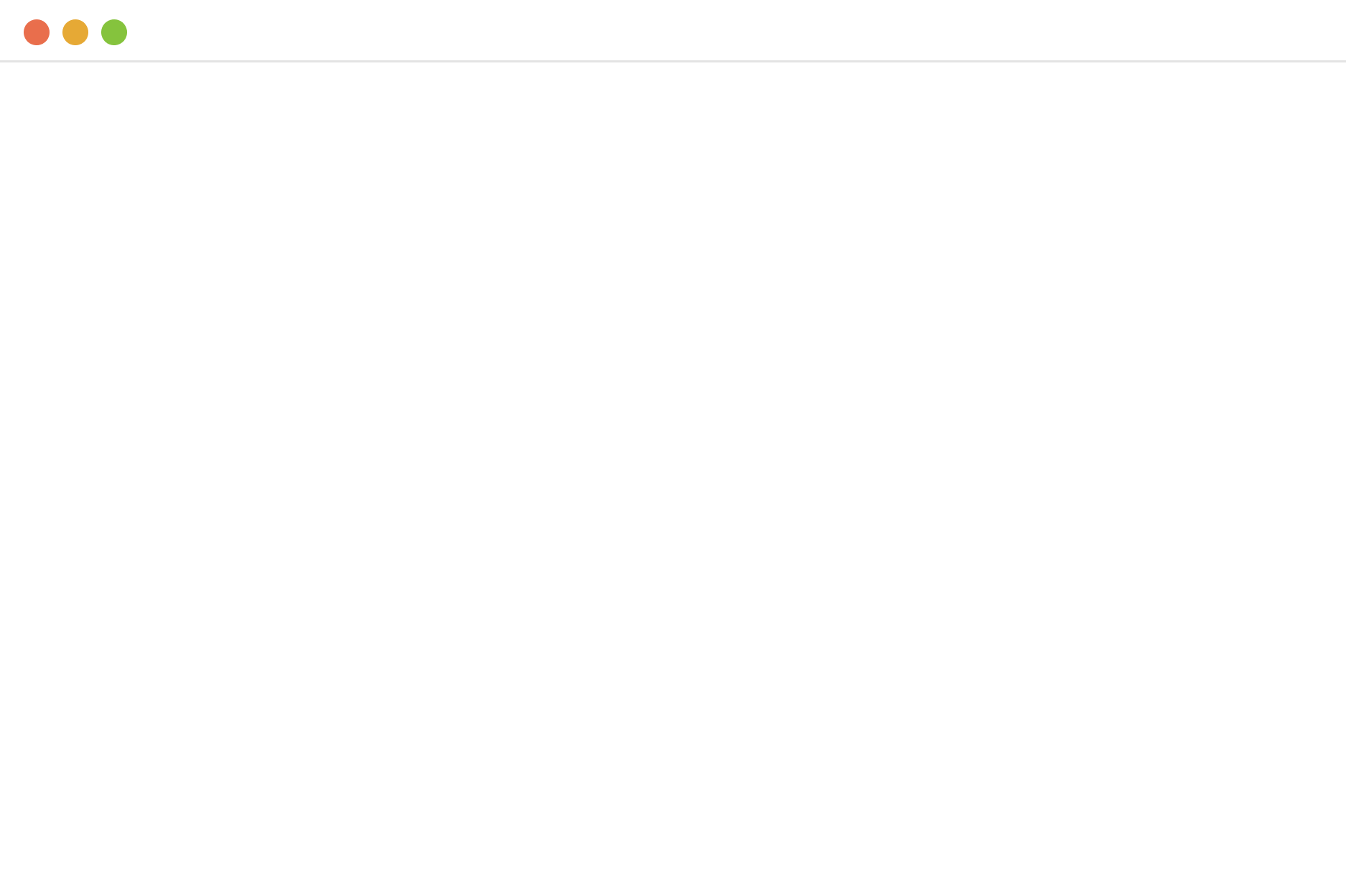
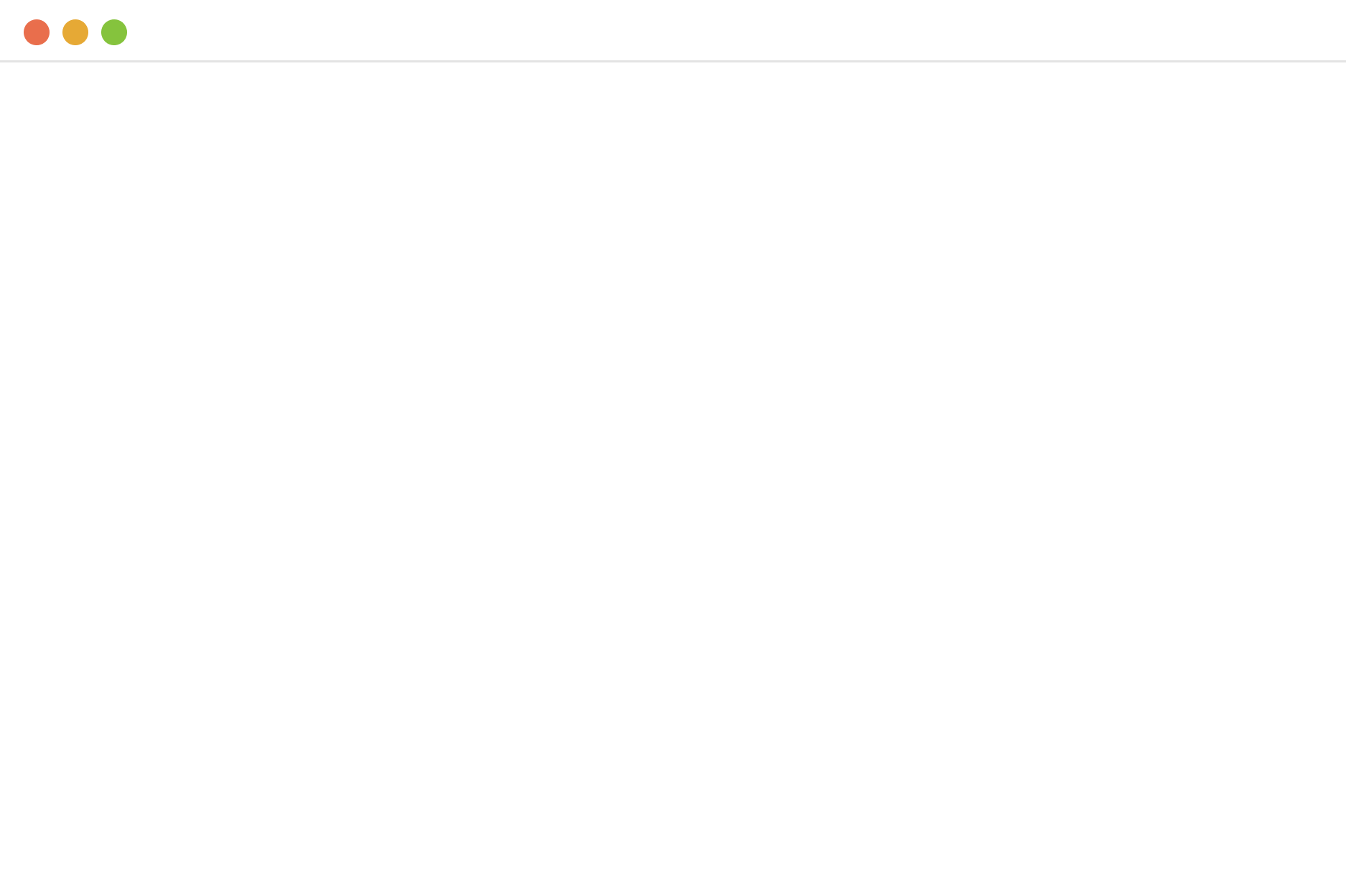
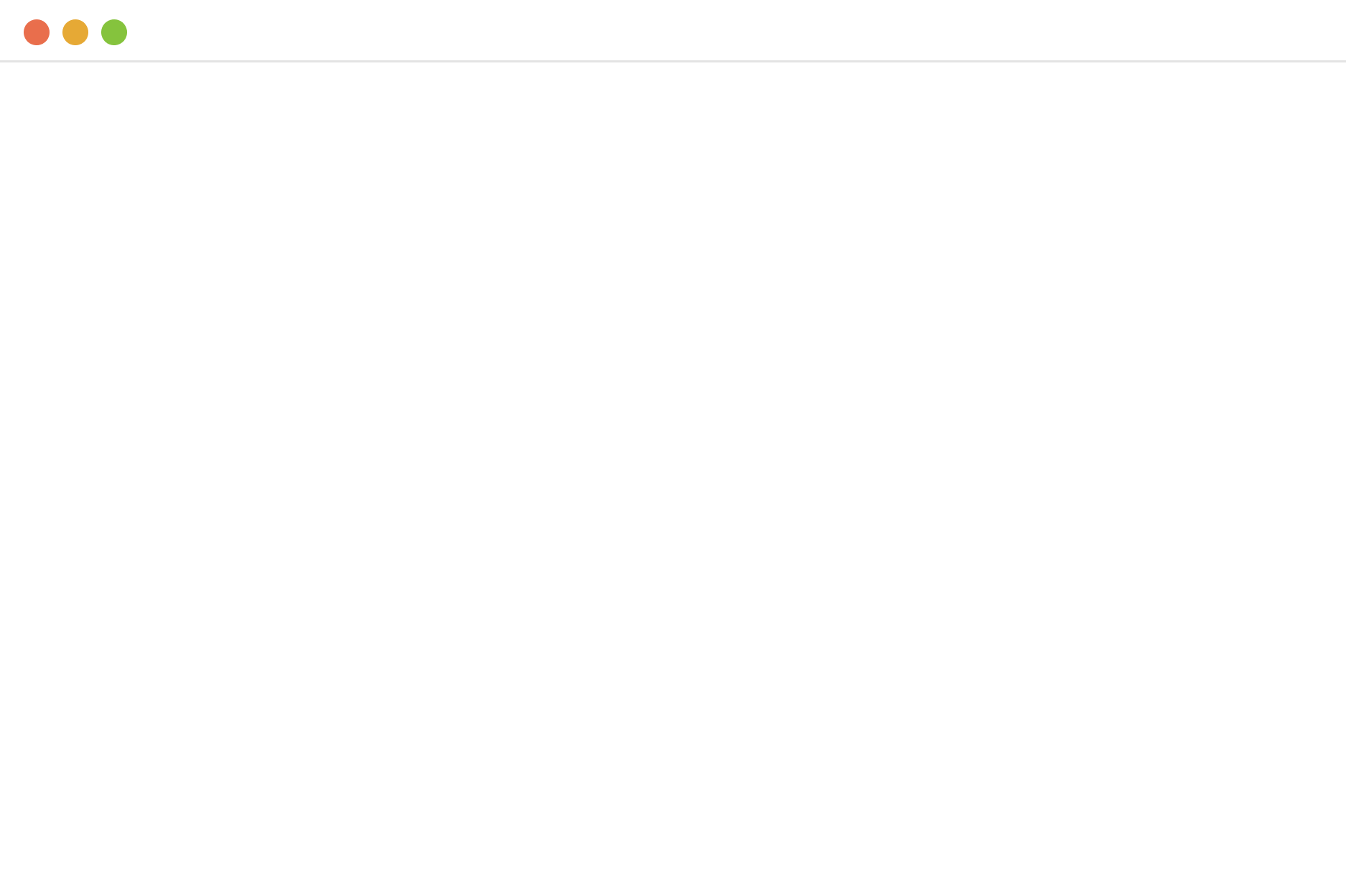
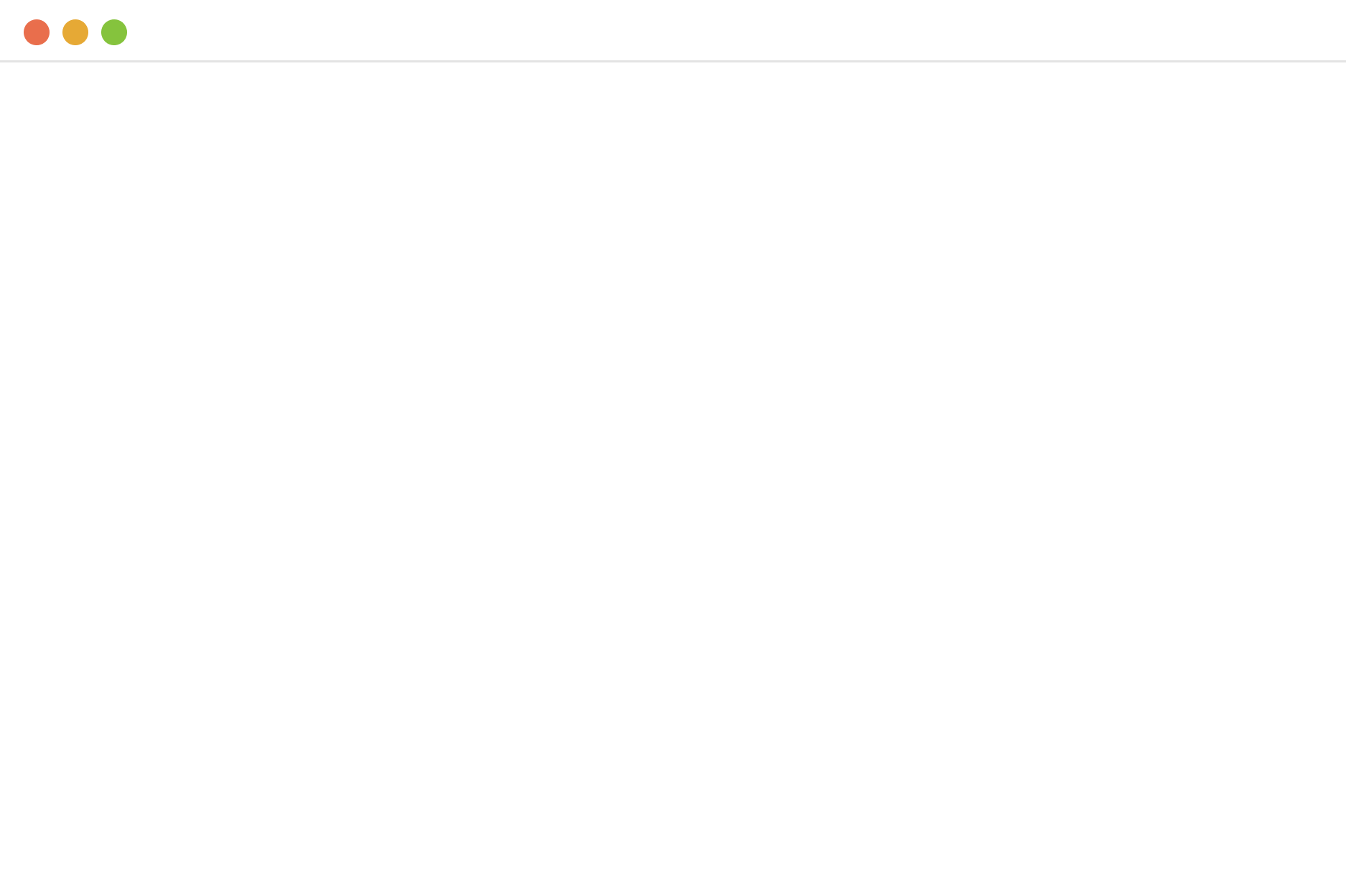
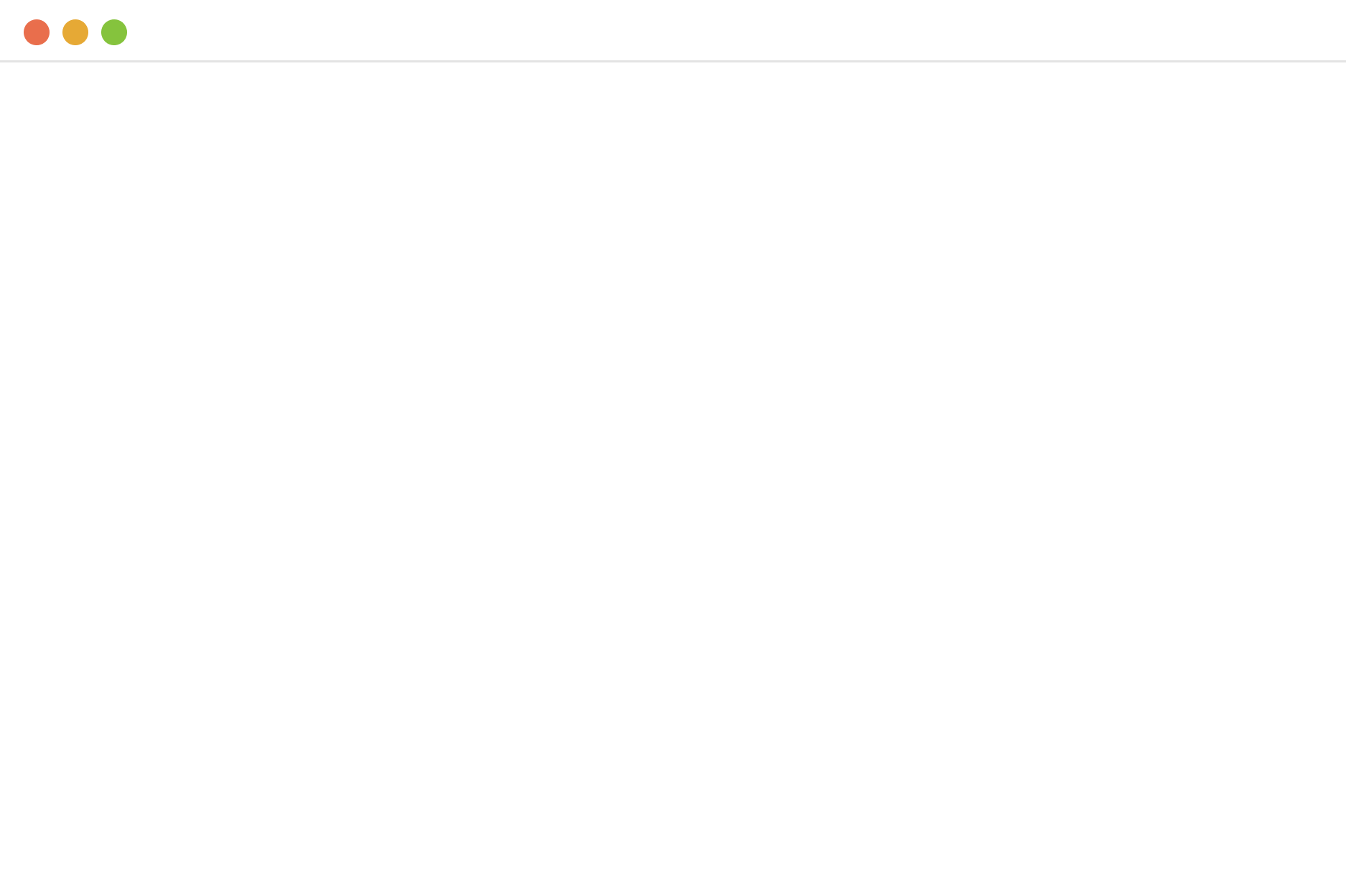
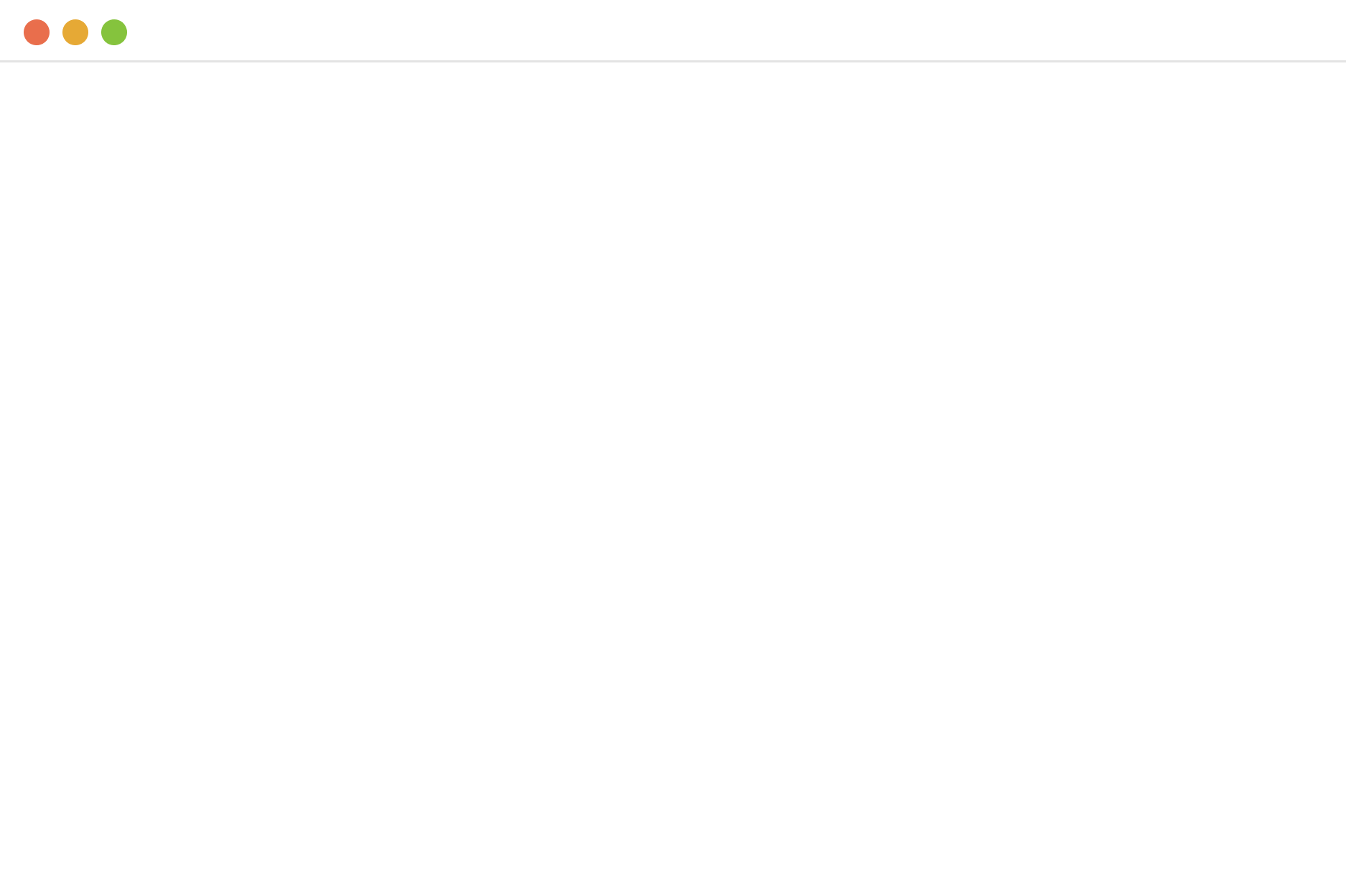
Focus on the right things for the whole business - from baseline analysis to implementation.
A clear thread from strategic to operational level.
A common system for continuous improvement throughout the organization, even when it is geographically dispersed.
Continuous improvement becomes a natural and integral part of the business, whether the approach is based on PDCA, DMAIC, Lean, Six Sigma, 8D or combinations of these.
Employees are committed and involved, ensuring that improvements are implemented and adhered to.
Conclusions and documentation are easily accessible.
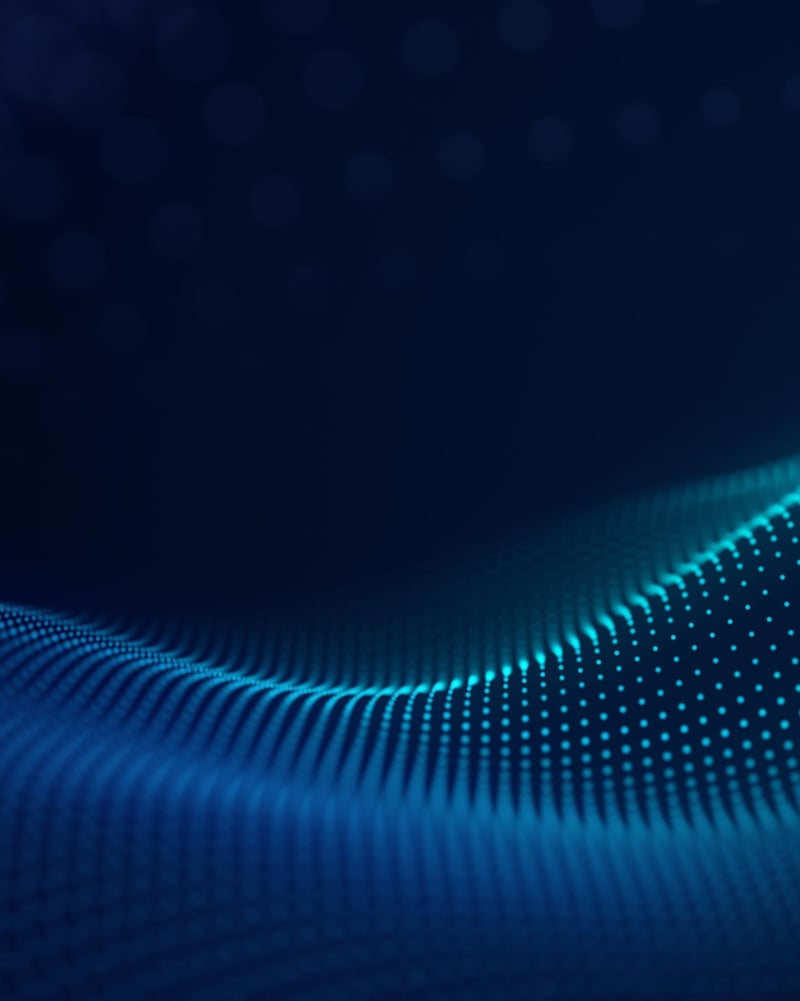
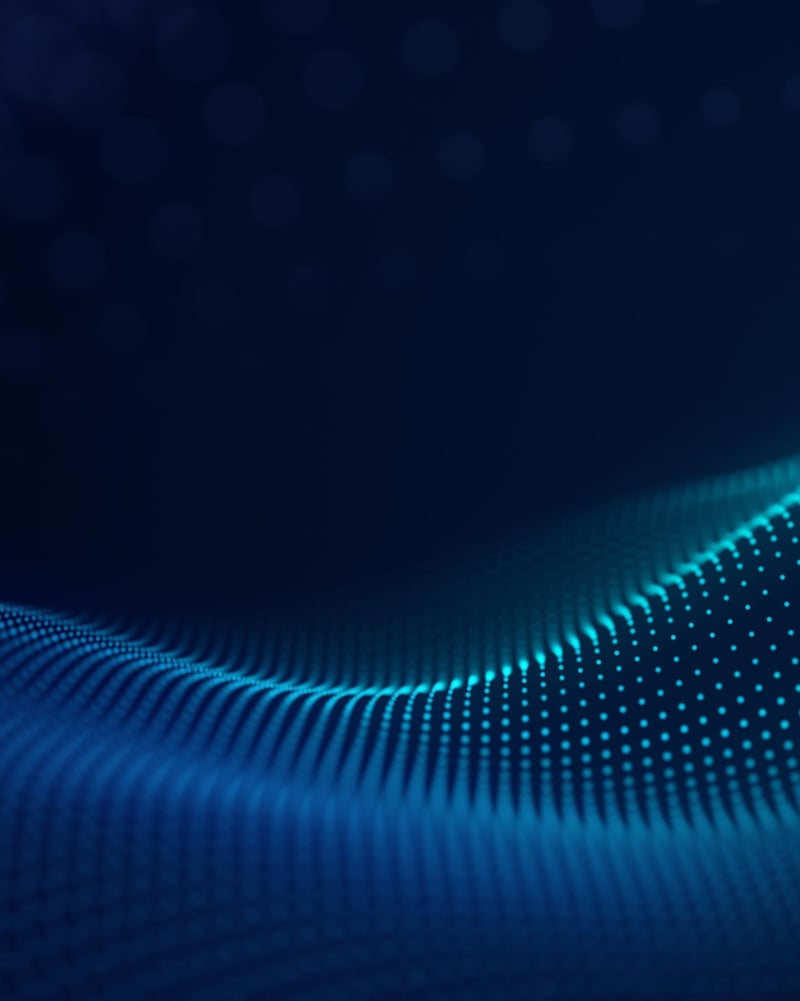
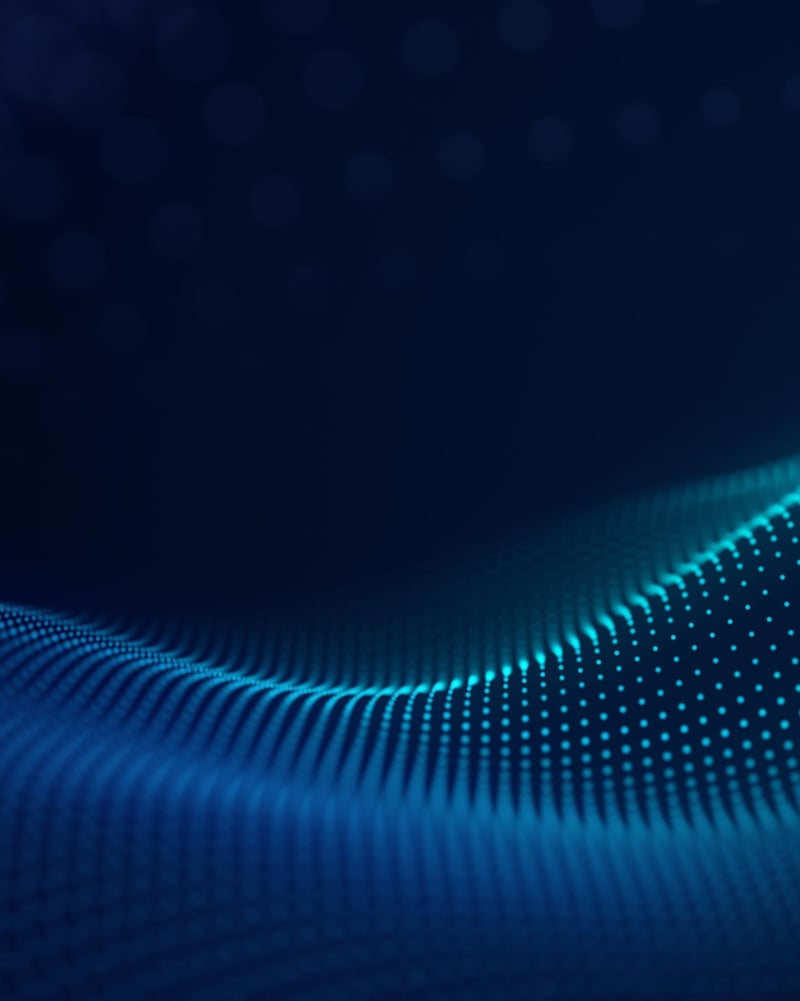
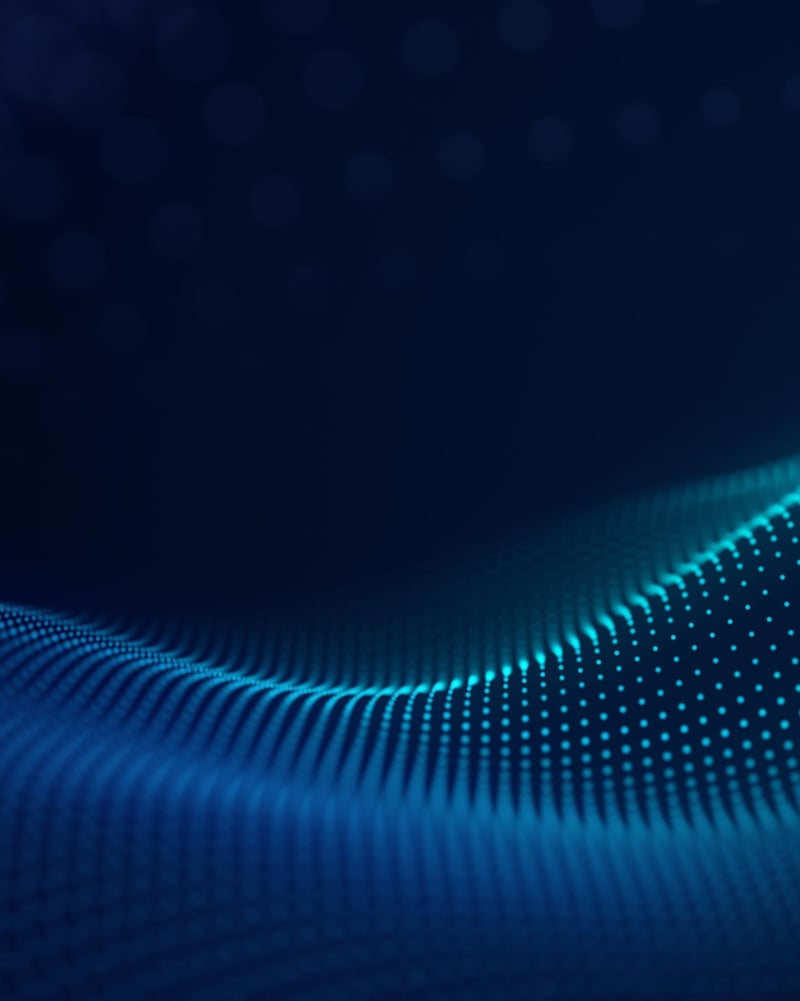
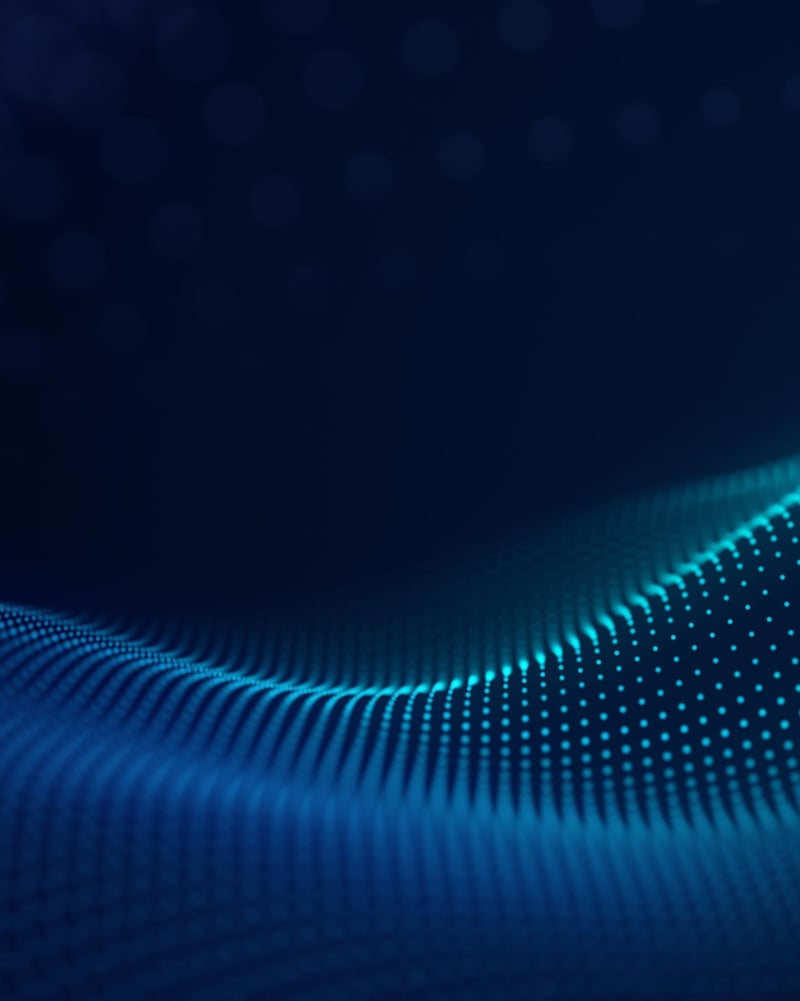
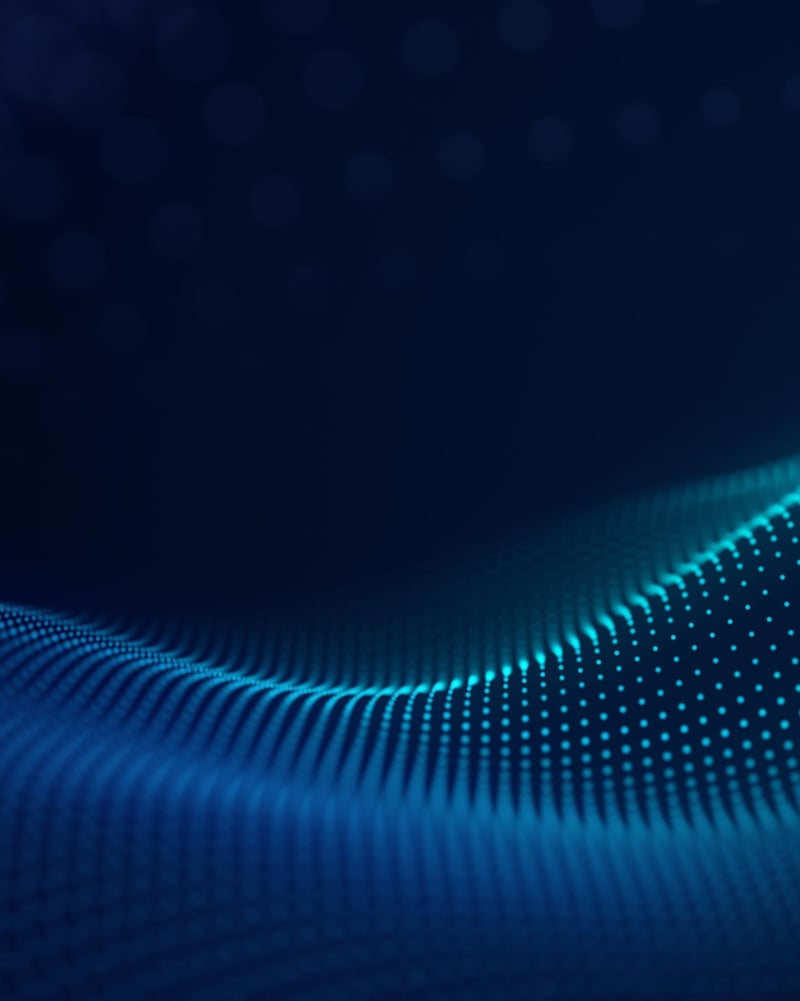
Part of a
comprehensive
solution
CANEA Document is one of five user-friendly modules in our CANEA ONE platform. The modules can be used as stand-alone modules and together form a comprehensive system for efficient business management; linking strategies, projects, processes, cases and documents.
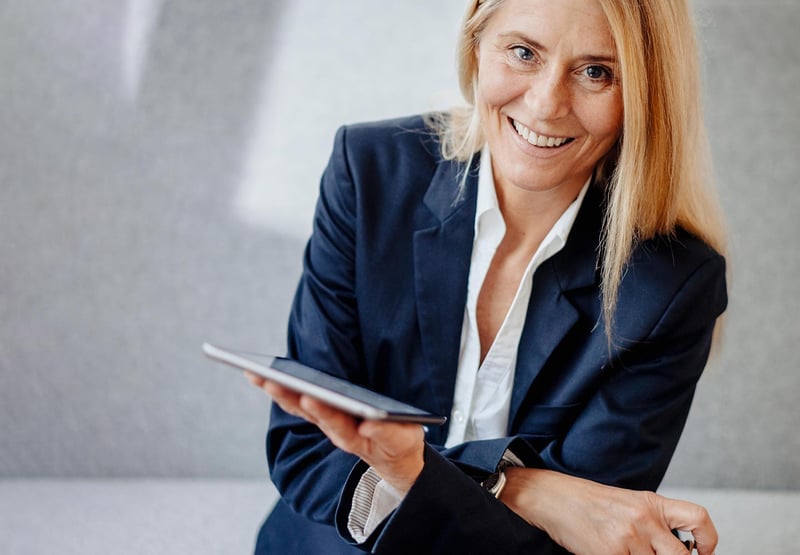
CANEA knows continuous improvement
We're passionate about continuous improvement - it's one of our core competencies. Our unique combination of proven IT solutions, experienced management consultants and highly regarded training courses means we have what it takes to help you sharpen your improvement initiatives, regardless of your current level of maturity or the methods you currently use.
Some of our clients
Canea has helped hundreds of organizations become both more efficient and more profitable. Here are some examples of what we've worked on so far.

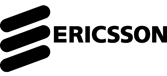
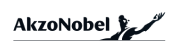
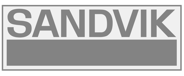
-1.png?height=76&name=G%C3%B6teborgs-Stad-logo-SV%20(1)-1.png)
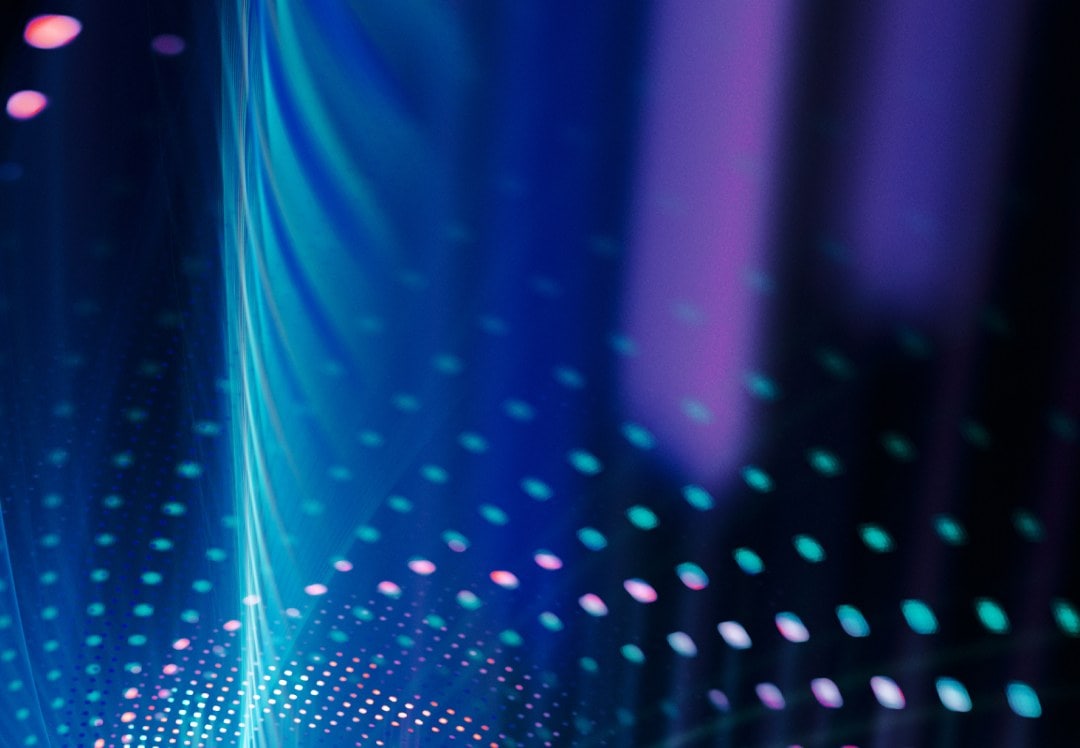