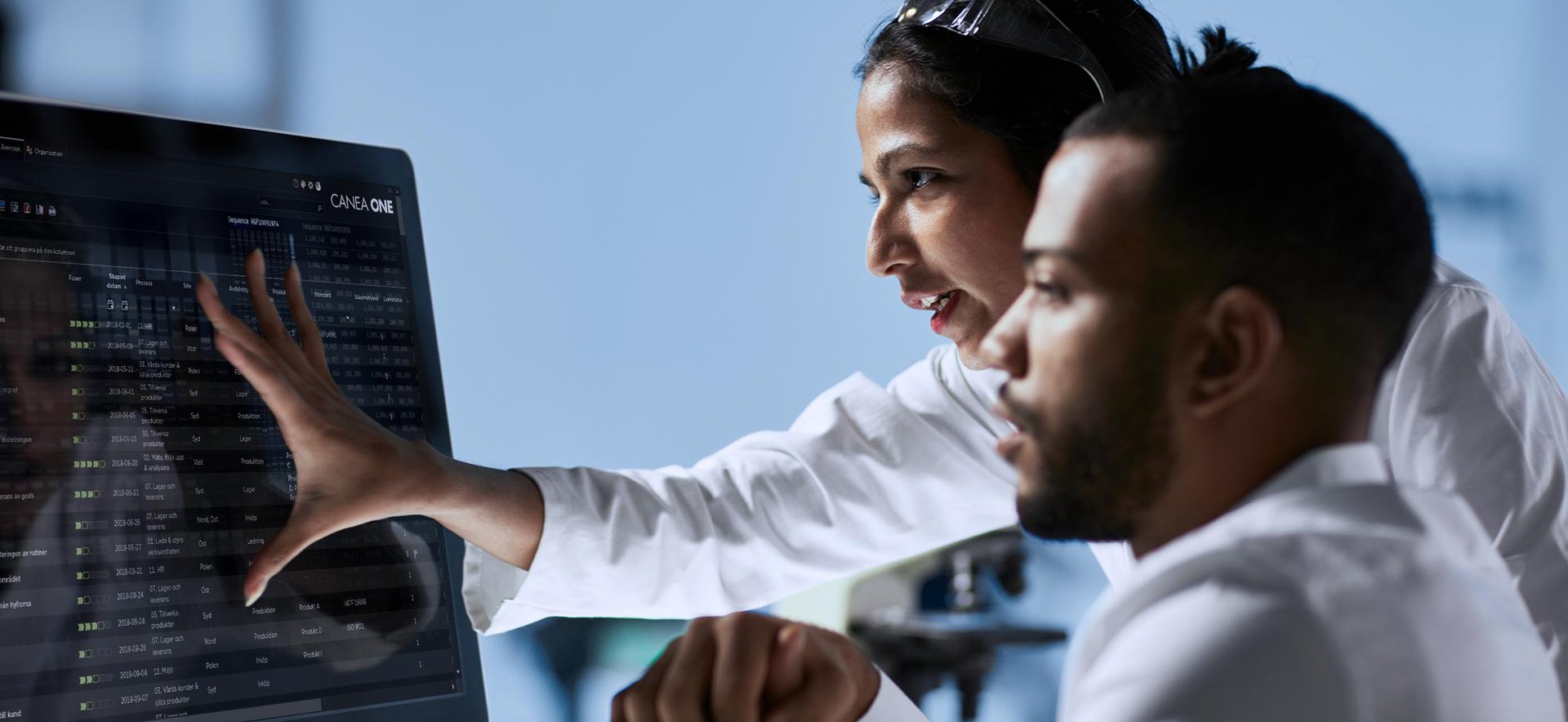
CAPA – an essential part of Good Manufacturing Practice GMP
Cut the cost of non-compliance work and ensure compliance with CAPA.
Background
In the life sciences – medical devices, pharmaceuticals and biotechnology – it's essential to comply with GMP (Good Manufacturing Practice). The CAPA (Corrective Action and Preventive Action) method ensures that the work to identify the root causes of deviations is carried out in a systematic way. The result is a corrective action that also ensures that the error does not occur again.
Challenges in the medical technology, pharmaceutical and biotechnology sectors
One challenge is to get employees to carry out the non-compliance work in a structured way and within the set time. There are also far-reaching industry requirements for traceability of what has been done, plus that approvals, or other important actions, should be signed electronically so that it is possible to see who did what afterwards.
The CANEA ONE management system has clever features to ensure that root causes are investigated properly and in a timely manner and that CAPA work is carried out in accordance with the requirements.
How we have
solved the problems
Over the years, we have helped many clients digitize their CAPA processes by providing a system that ensures that corrective actions are carried out correctly and consistently, with the confidence that the same errors will not be repeated. Responsibility for the different parts of the process has been identified and everyone involved has been given clear roles with responsibilities and resources.
CANEA ONE produces easy-to-read reports that make it simple to share CAPA management with customers, suppliers, regulators and others. Smart rules guide how things are done; for example, in the event of a serious deviation, root causes should always be investigated using the 5Y methodology, or alternatively with Ischikawa/Fishbone diagrams or 8D.
CANEA ONE is a validatable system, which few other providers offer so far.
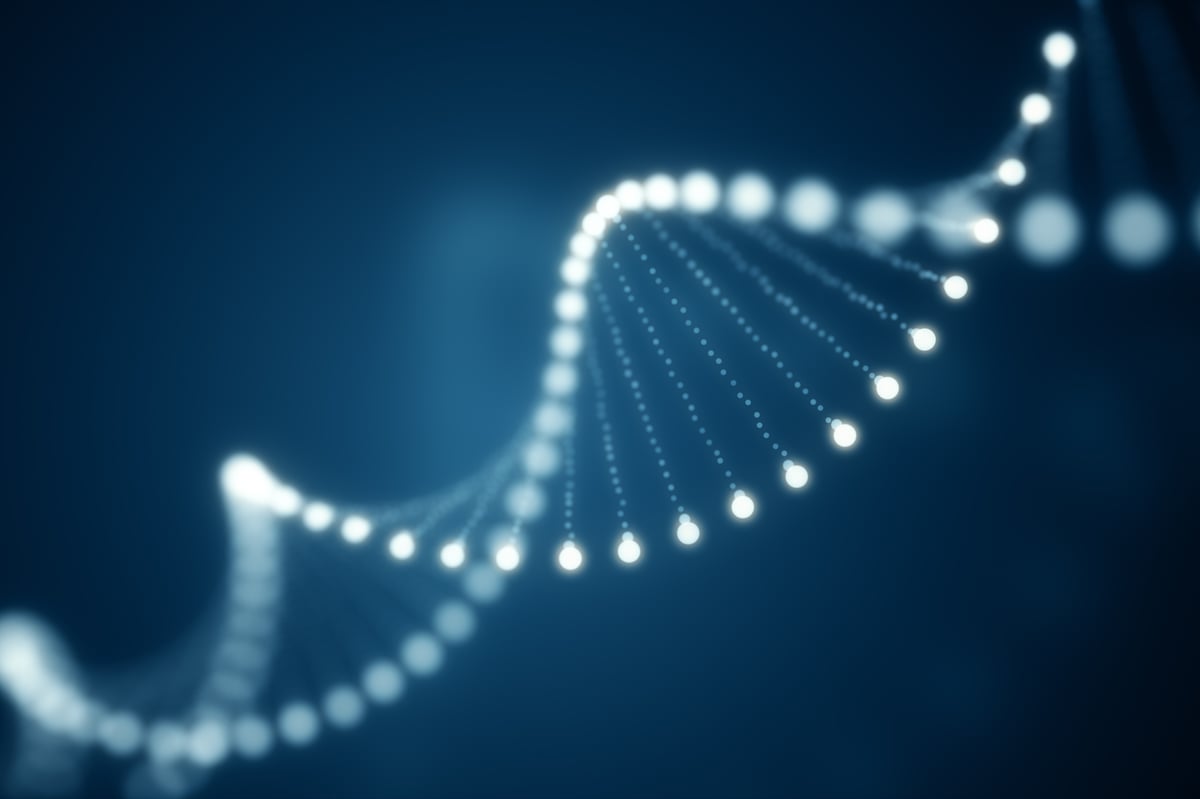
The best with CANEA ONE
CANEA ONE is currently used to manage everything from deviations, CAPA and complaints to audits, changes, supplier evaluations and risks. Customers can easily make adjustments, with sometimes necessary re-validations, directly in the system and without the need to consult experts. This simplicity in managing and using the system ensures a live and healthy eQMS that is appreciated by employees.
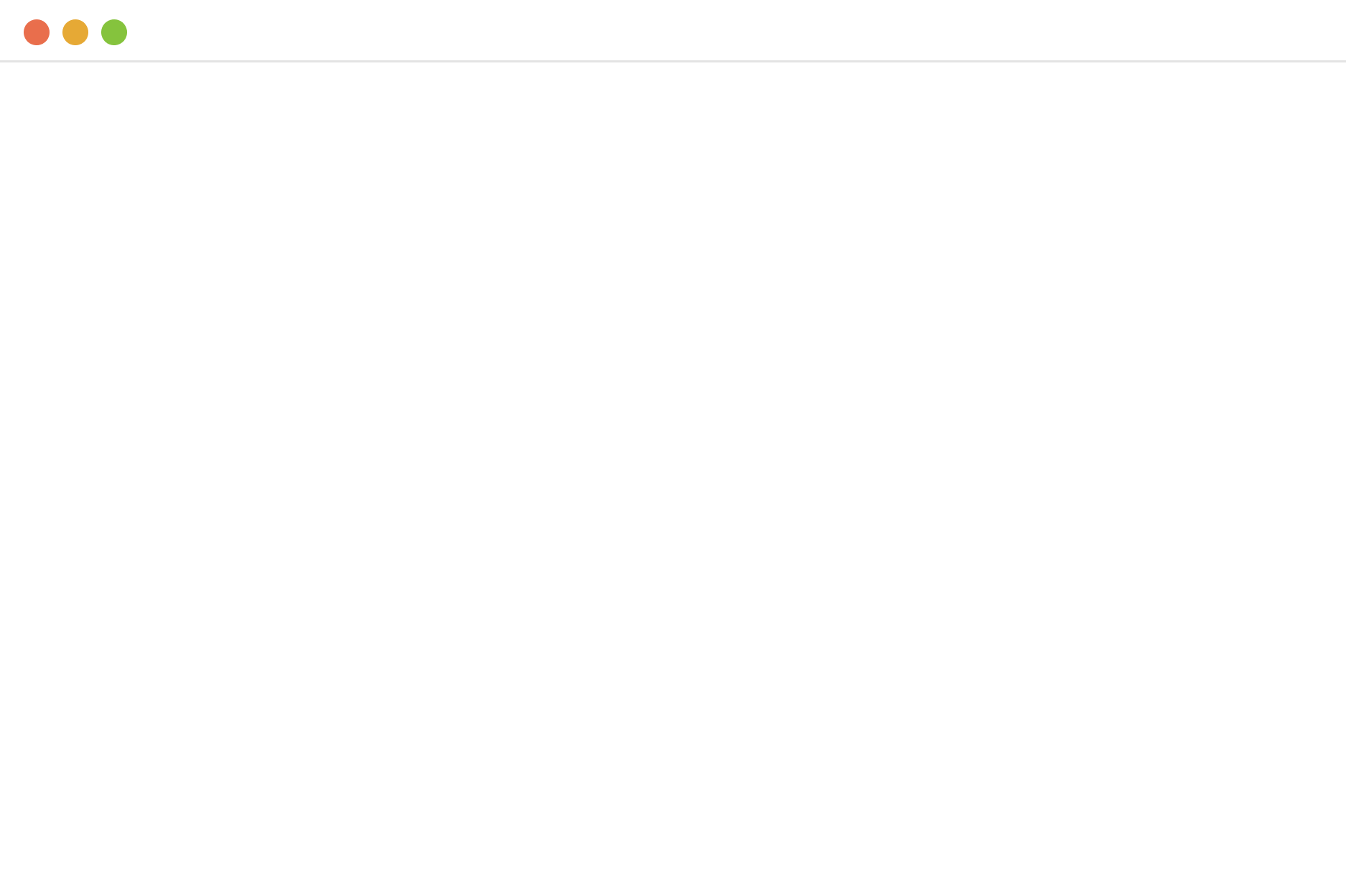
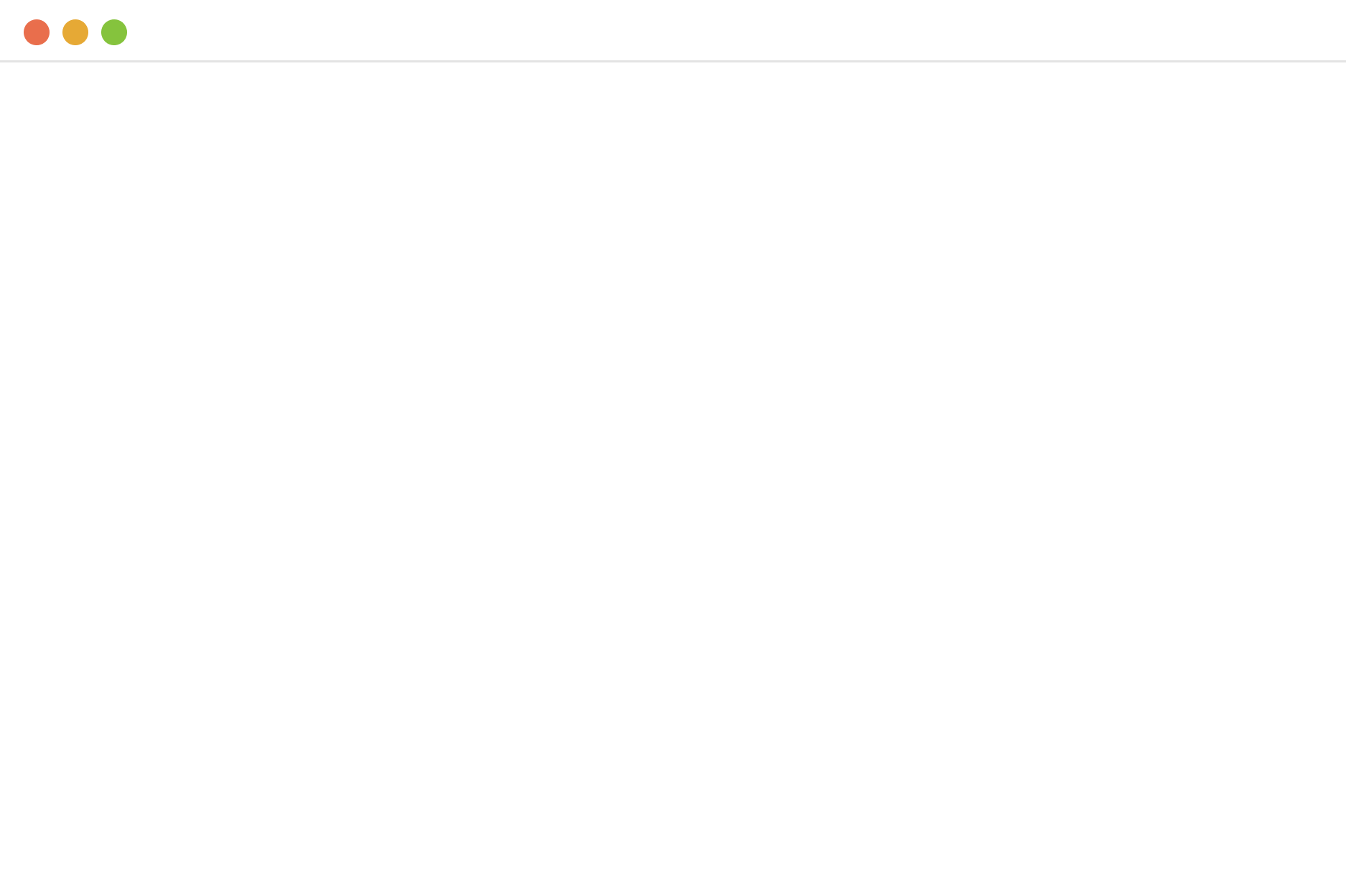
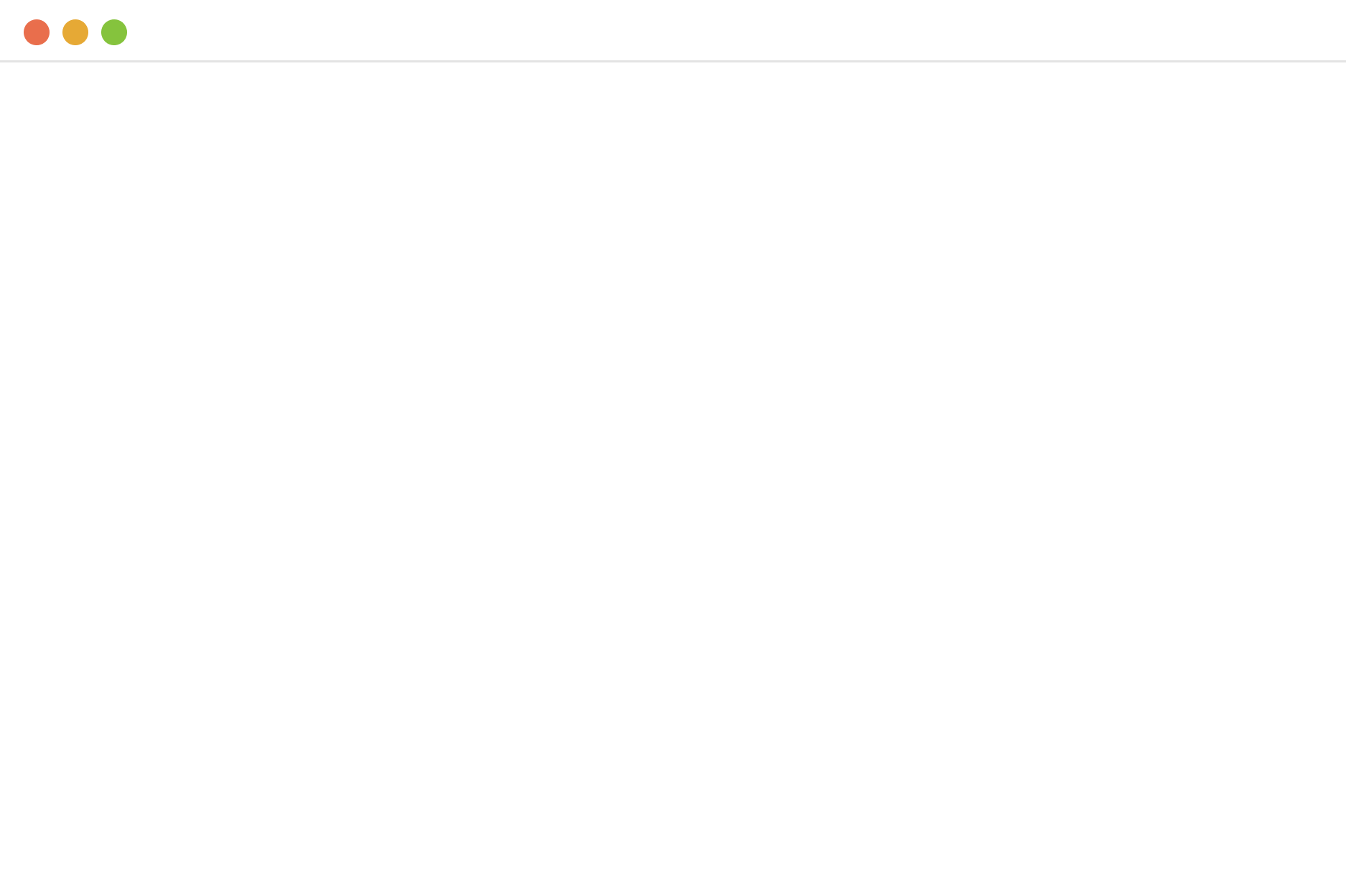
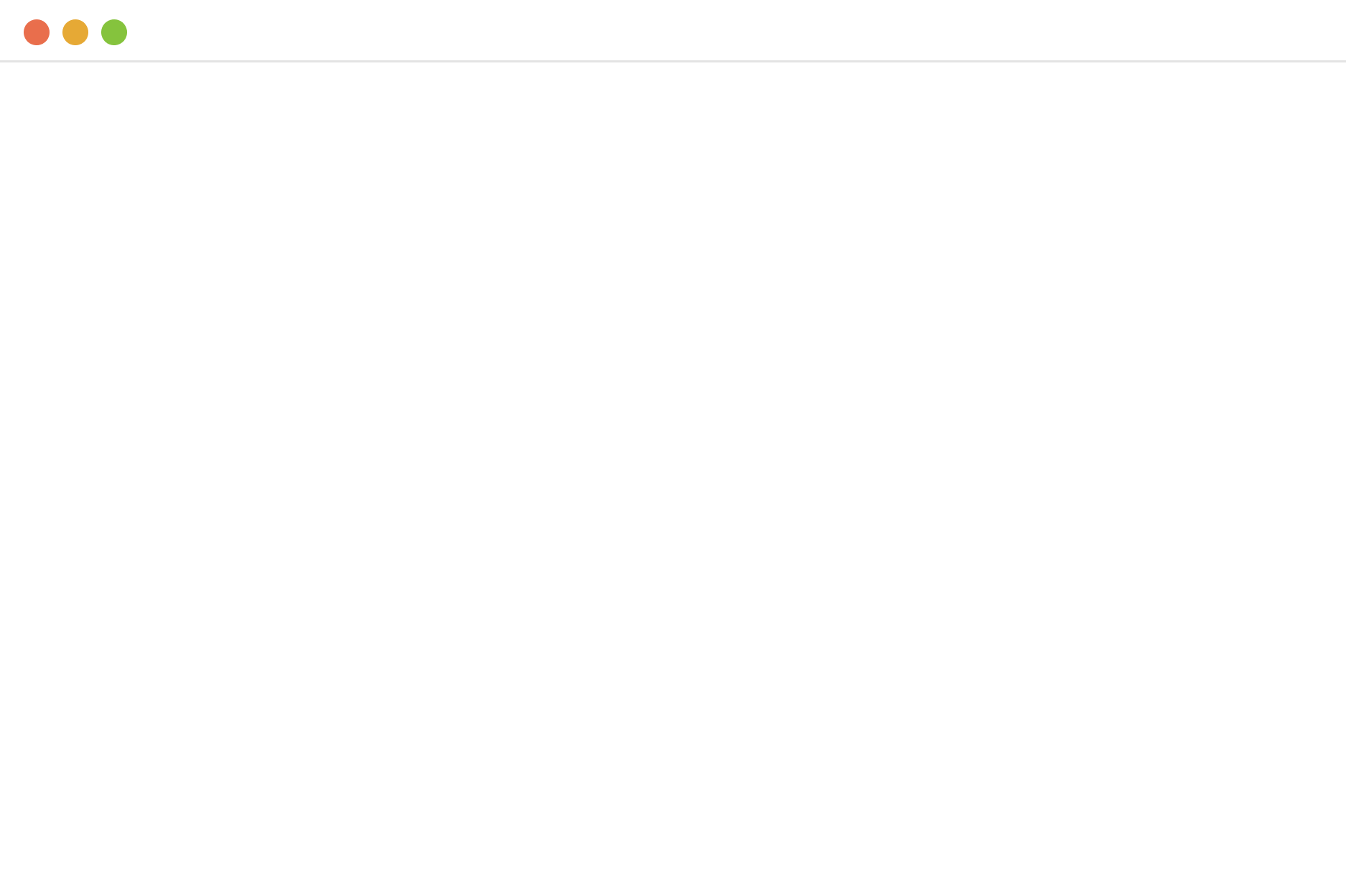
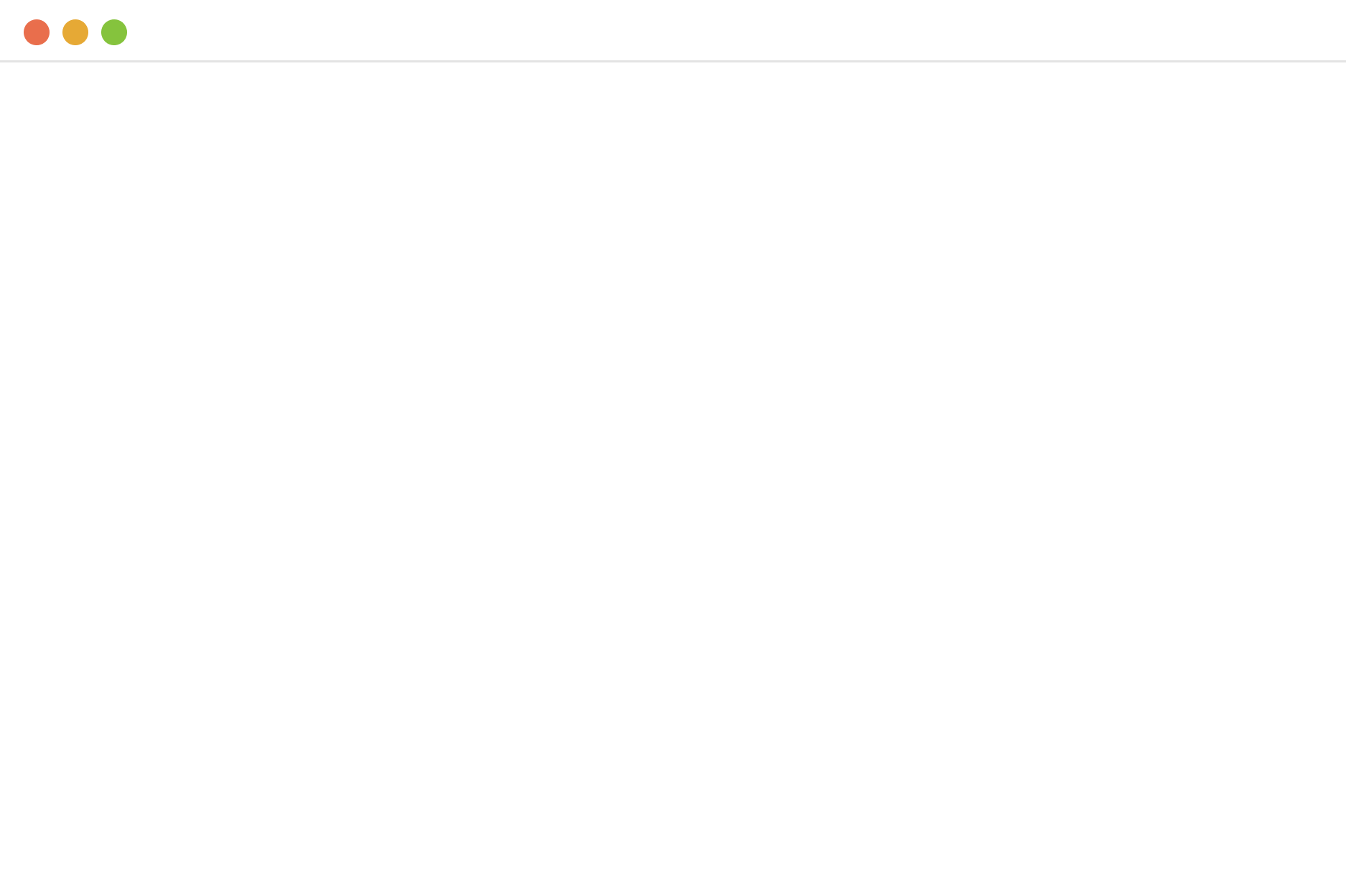
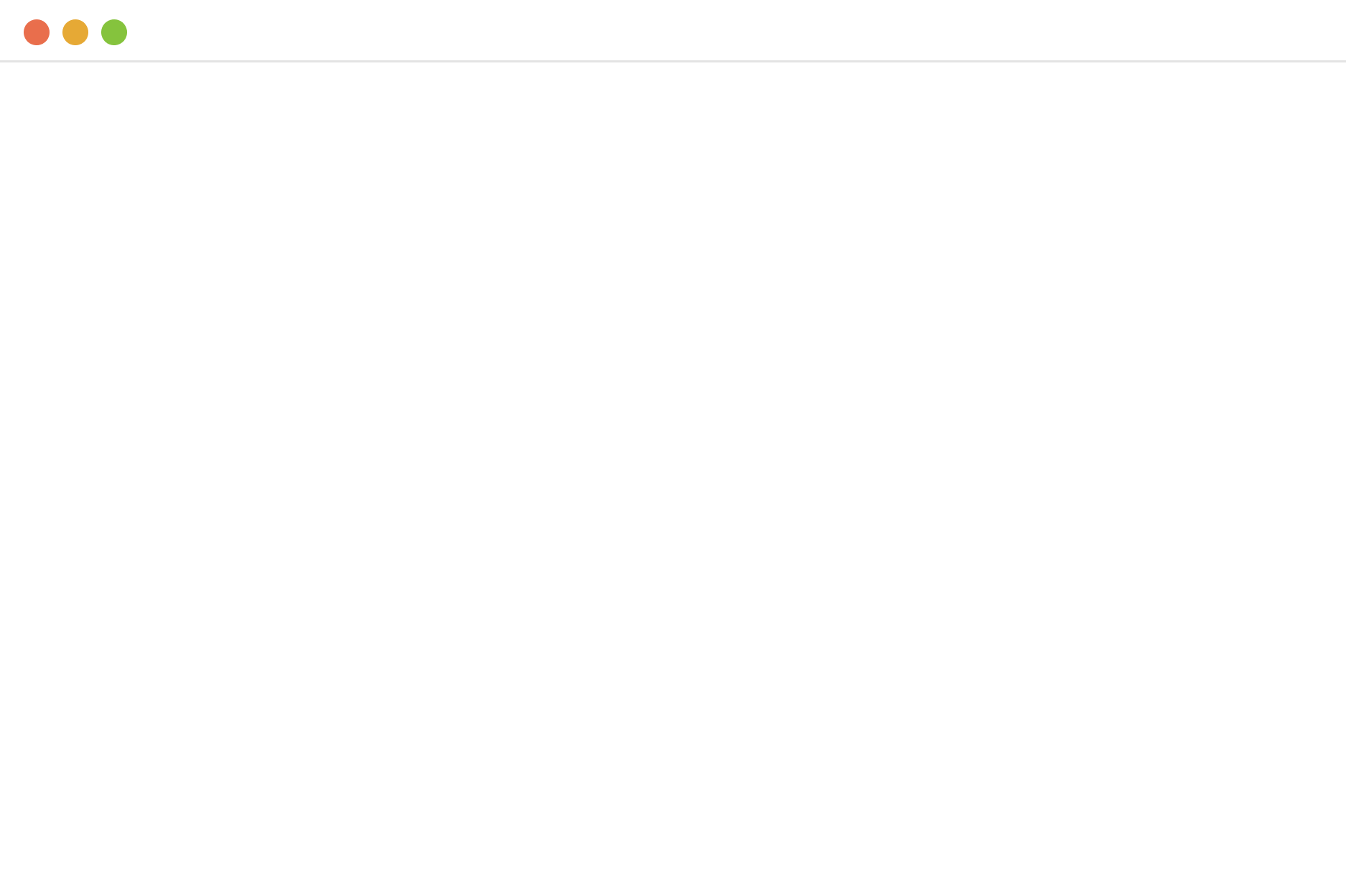
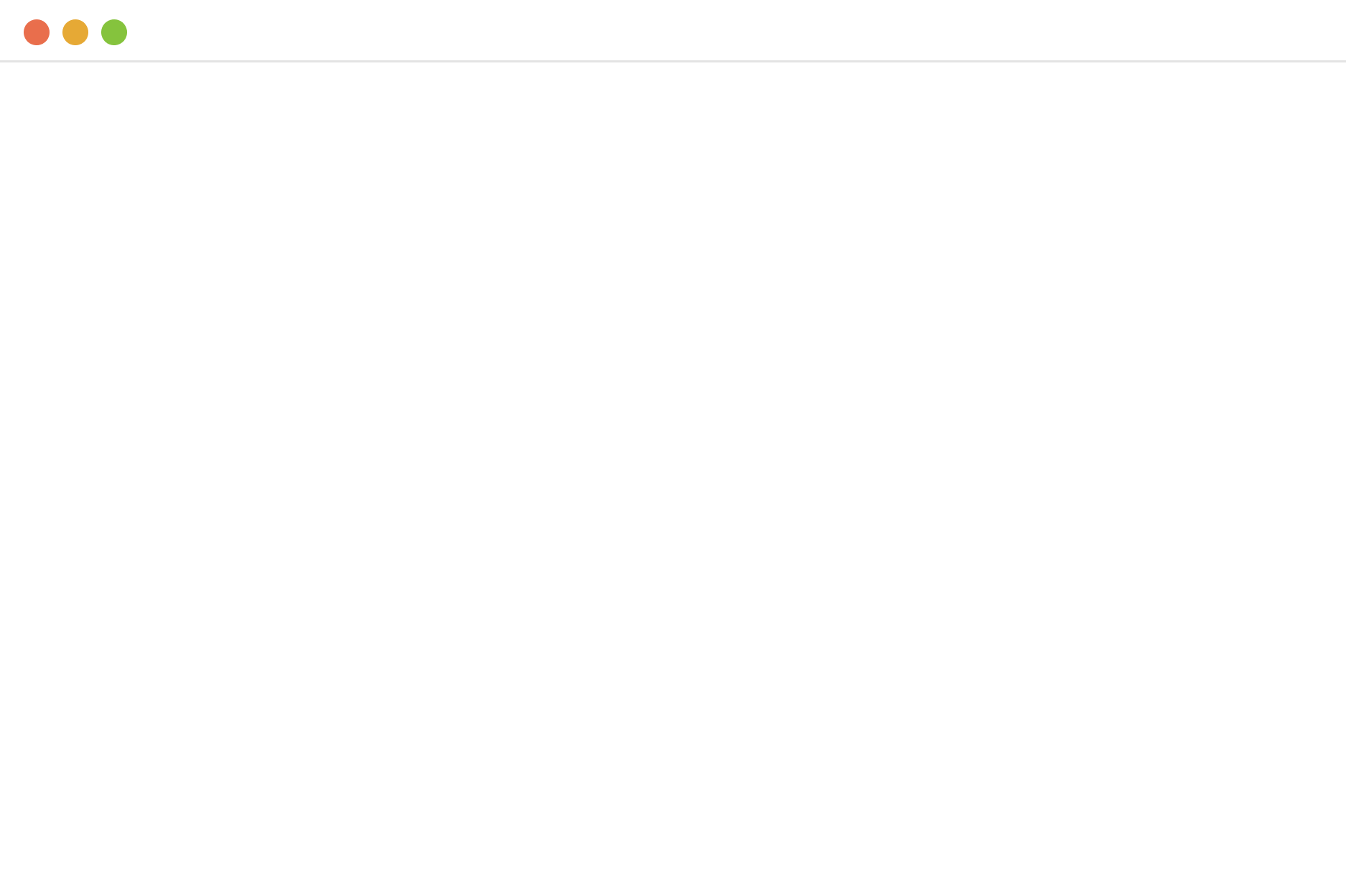
Using CANEA's security management, you can choose which employees can see what in a CAPA case.
It is easy to produce trends and summaries via graphical analyses; all the data needed can be easily obtained during an analysis.
The system keeps track of CAPA cases and sends reminders, partly via the user's home page but also via e-mail notifications.
Using the priorities set for different cases, in terms of the parameters "priority" and "urgency", it is easy to produce lists of which cases need attention first.
Corrective and preventive actions are handled smoothly by delegating and structuring them as sub-cases, where the responsible person can act according to a defined process with checklist, documentation etc. The responsible person can verify the actions before closing a CAPA.
Of course, there is full traceability of all events for each CAPA - the audit trail - but it is also easy to filter by type of event, time and/or person or to search events based on the content of the case data.
Using built-in templates, the system produces the type of CAPA report required, either in the form of a Word document or as a PDF file. It is also possible to generate reports with different appearance and content for different purposes.
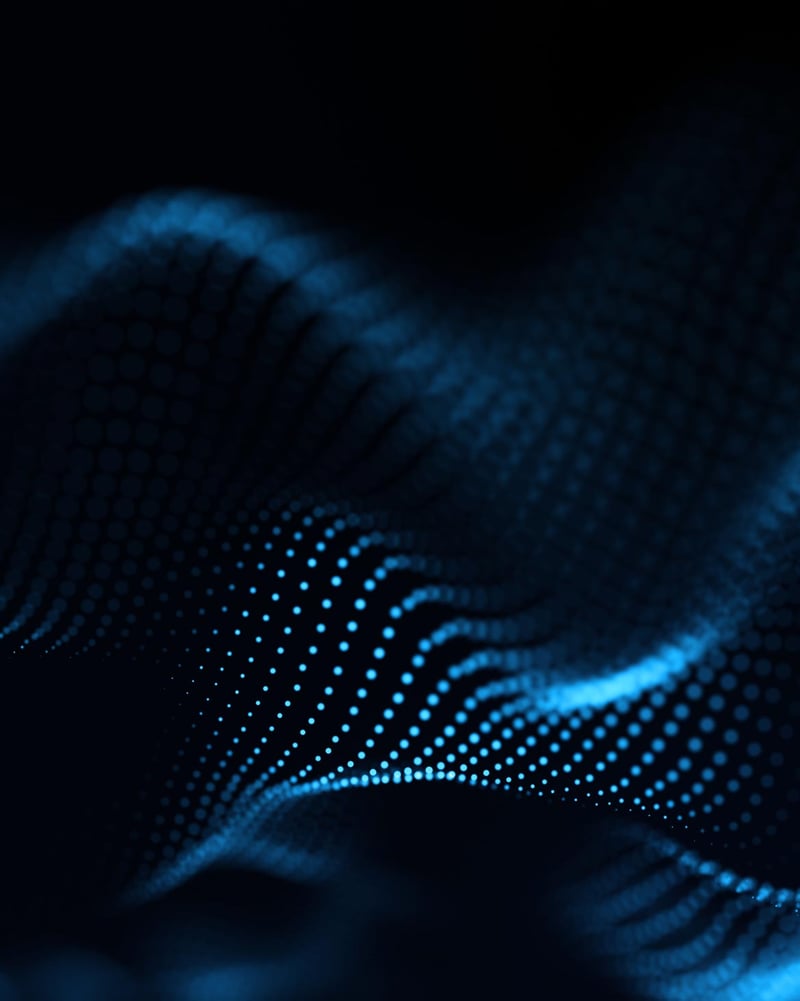
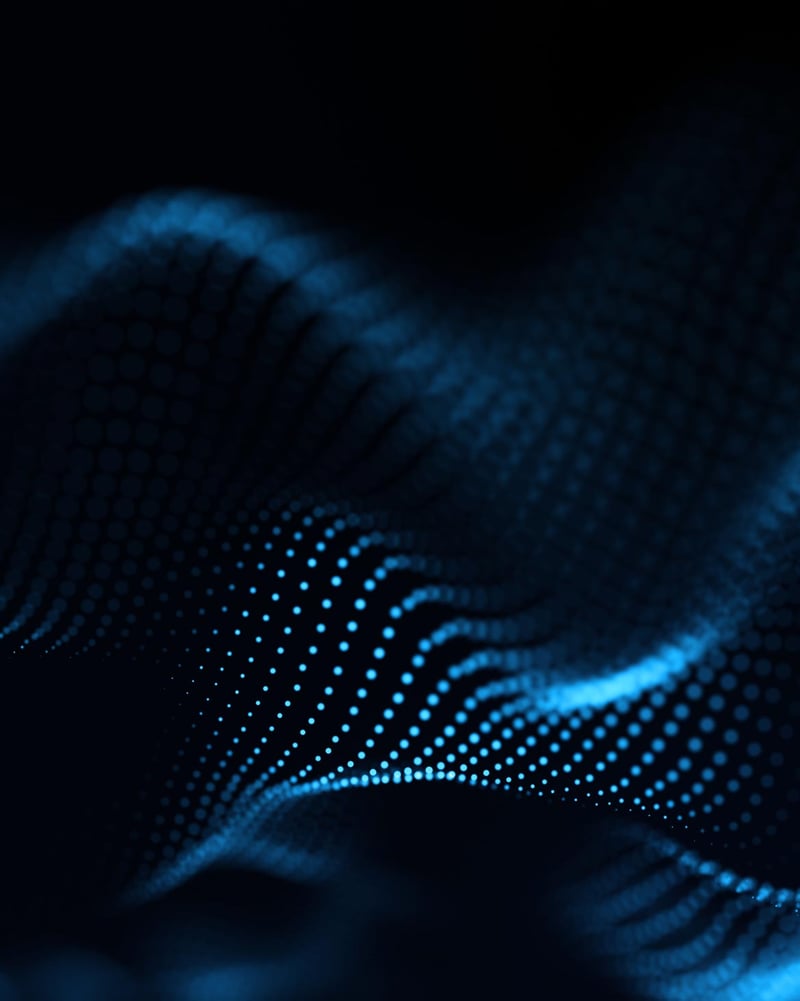
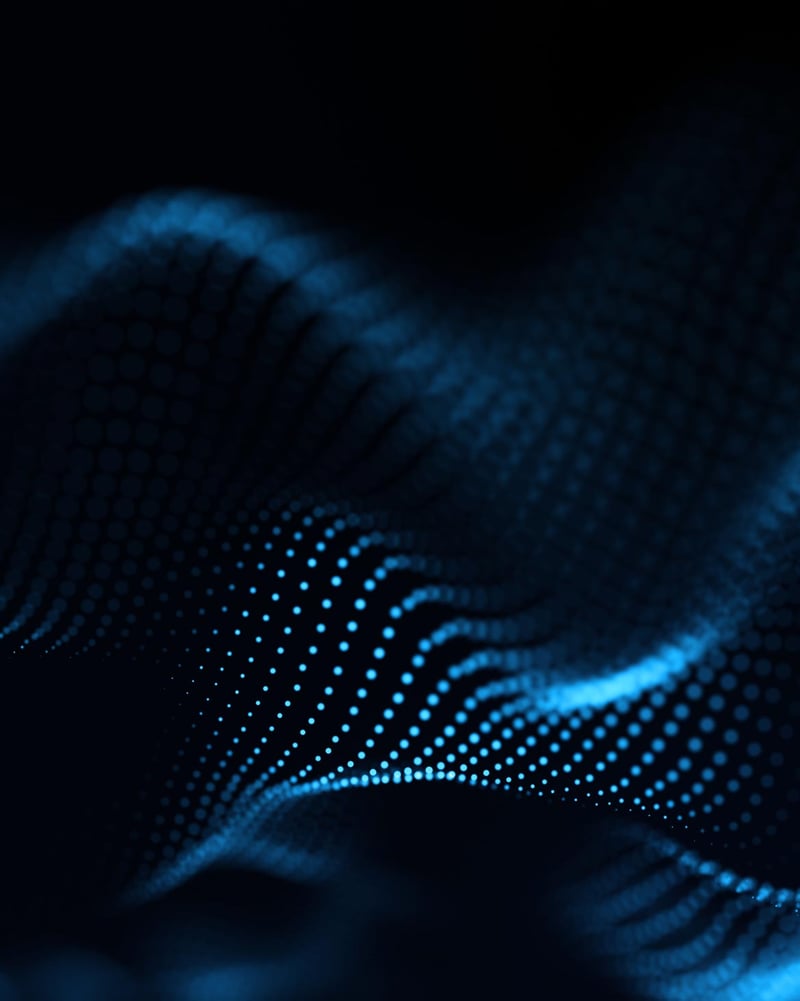
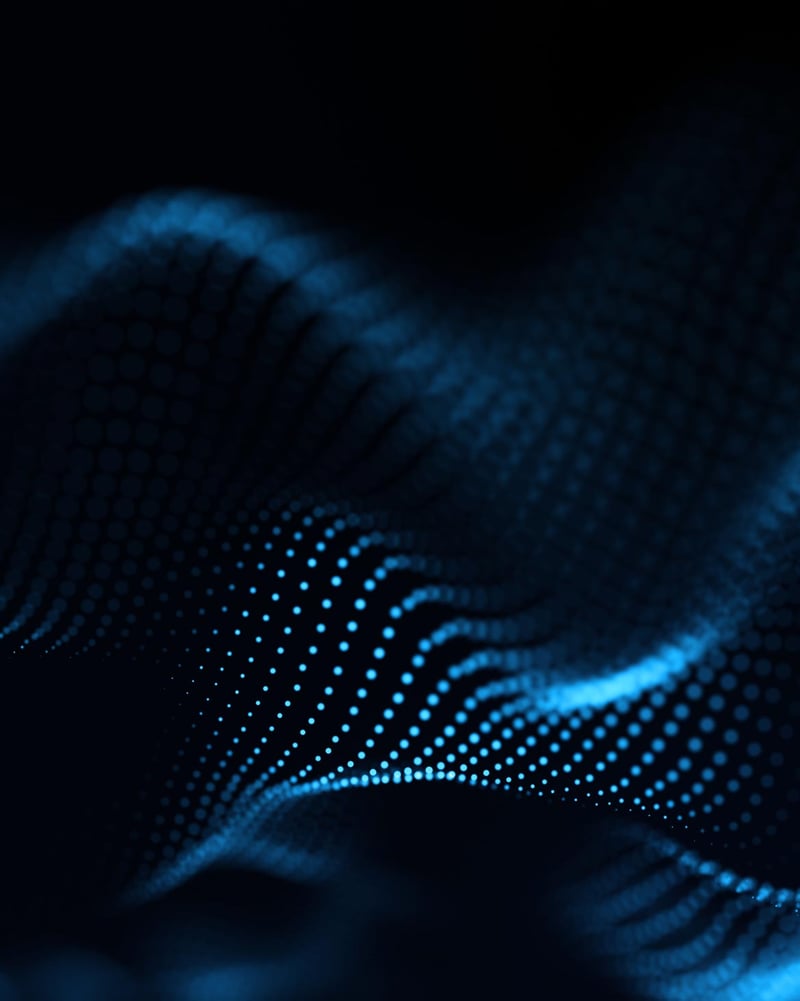
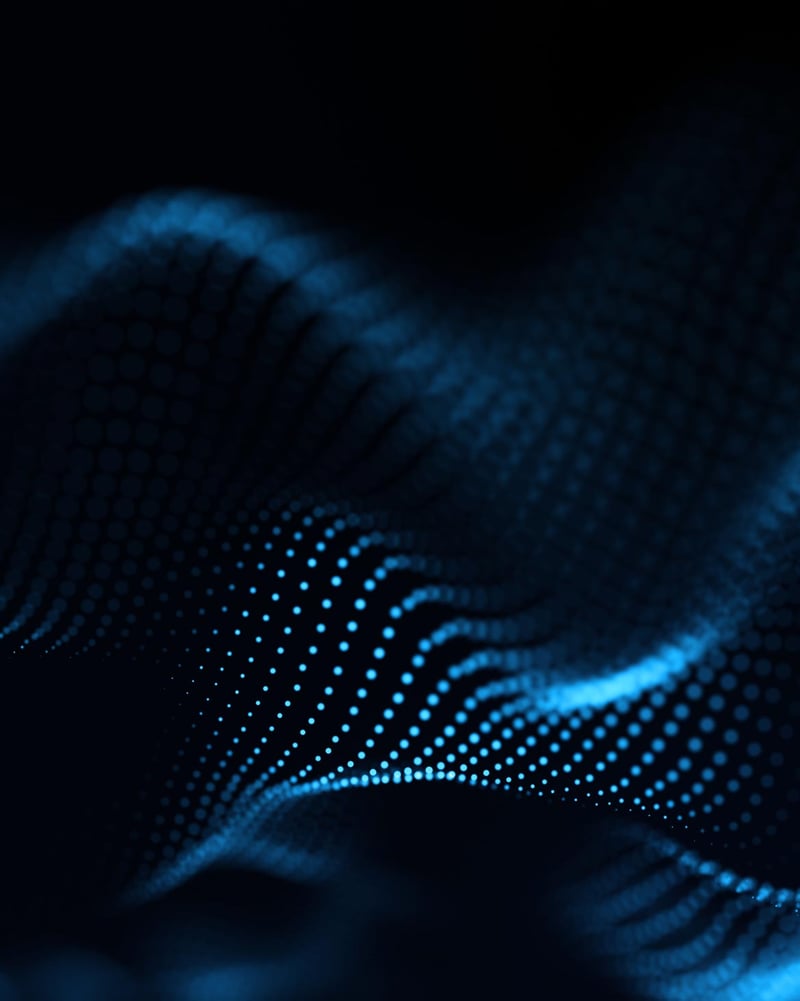
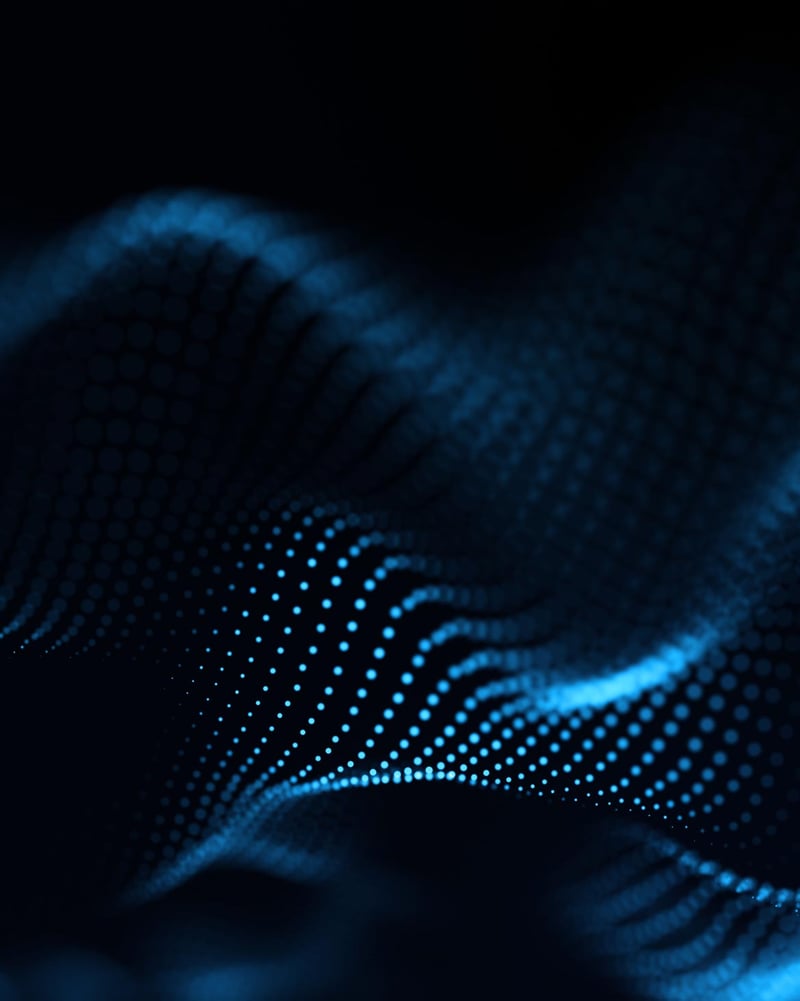
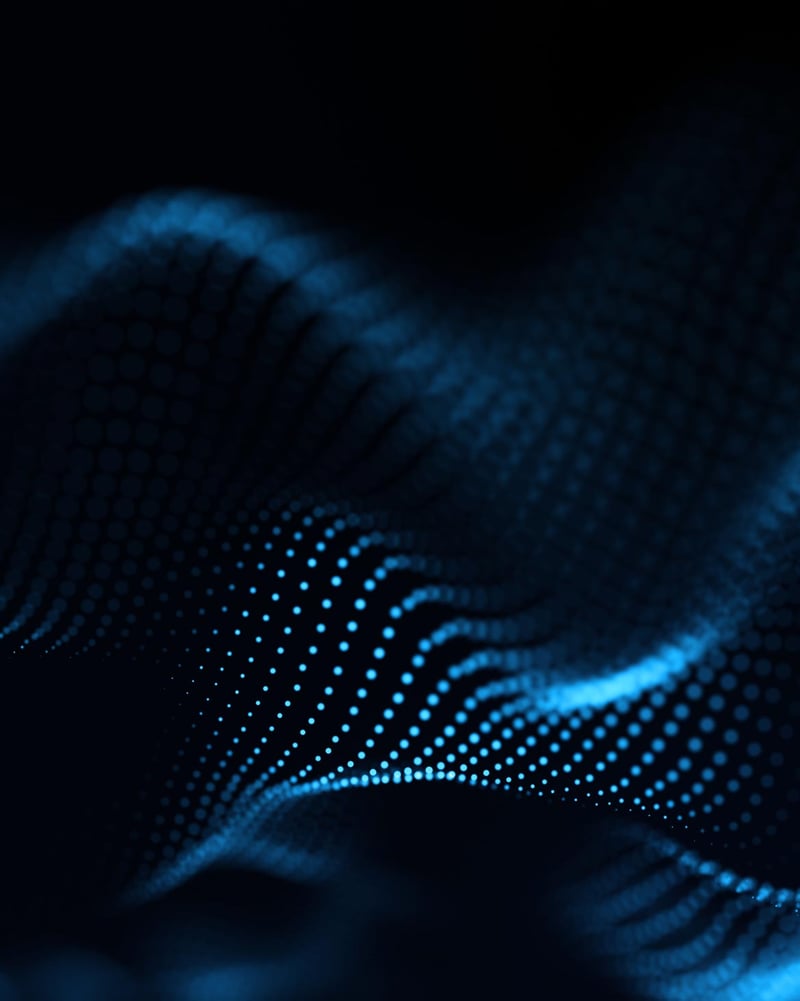
Part of a comprehensive solution
CANEA Workflow is one of five user-friendly modules that make up our CANEA ONE platform. The modules can be used as stand-alone modules and together form a comprehensive system for efficient business management; linking strategies, projects, processes, cases and documents.
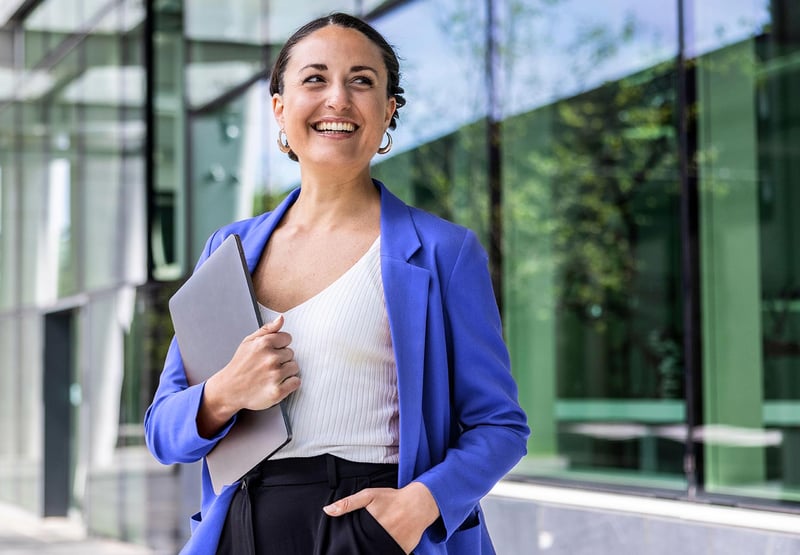
The benefits of CAPA
Built-in workflows for corrective actions and changes, for example, create greater efficiency, better process compliance and increased quality assurance in management. Through monitoring and statistical functions, deviations such as product defects can be systematically analyzed and eliminated. The ability to both solve root problems and prevent them ensures the quality and safety of processes and products. Decision support is provided through visualization, monitoring, reporting and analysis of collected data.
CANEA ONE is simply a user-friendly and stable system that effectively helps you to implement and evaluate your quality work.
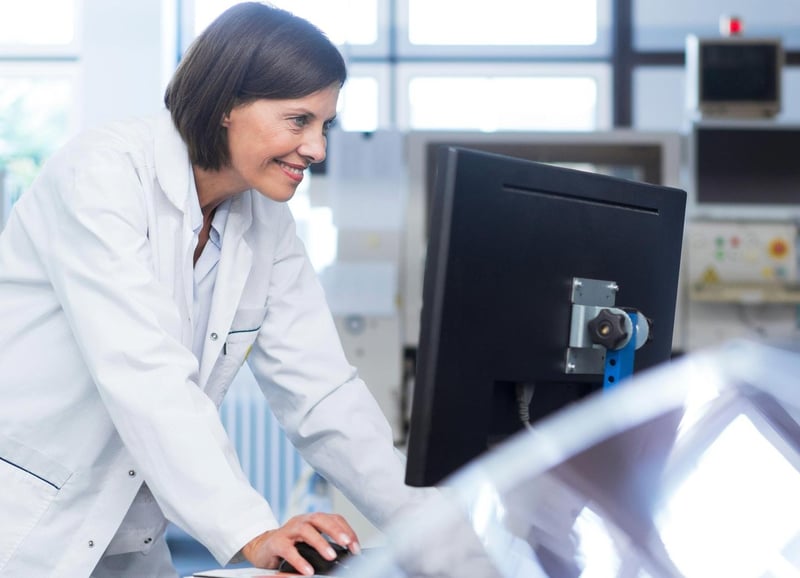
CANEA knows CAPA
We're passionate about continuous improvement - it's one of our core competencies. Our unique combination of proven IT solutions, experienced management consultants and highly regarded training courses means we have what it takes to help you sharpen your improvement initiatives, regardless of your current level of maturity or the methods you currently use.
Some of our clients
Canea has helped hundreds of organizations become both more efficient and more profitable. Here are some examples of what we've worked on so far.

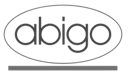
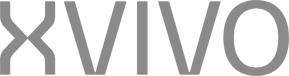
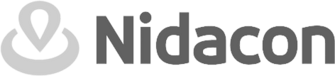
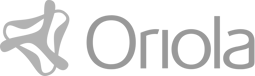
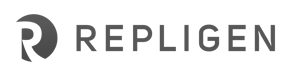
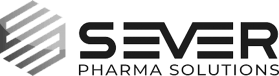

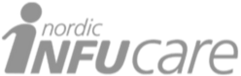
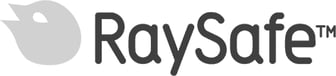
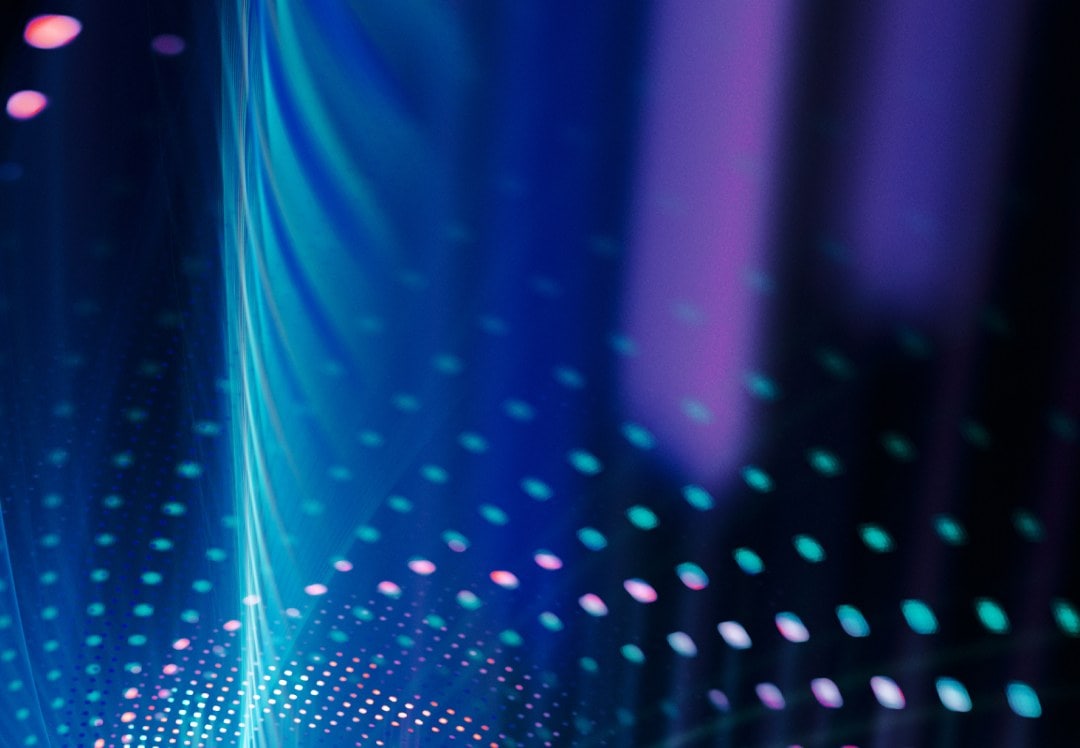
Want to know what we can do for you?
We have been helping companies with CAPA - an essential part of good manufacturing practice GMP - for 30 years cutting the cost of non-compliance work and ensuring compliance with CAPA.